Prin adaptarea corespunzătoare a debitului livrat la cererea fluctuantă de aer comprimat, fazele mari consumatoare de energie, și prin urmare costisitoare, de încărcare parțială pot fi eliminate aproape total.
Prin urmare, controlerul compresorului joacă un rol esențial în asigurarea eficienței energetice optime.
Compresoarele care funcționează la mai puțin de 50% încărcare ar trebui să tragă semnale puternice de alarmă în ceea ce privește pierderile însemnate de energie.
Mulți utilizatori nici nu sunt conștienți de acest lucru deoarece compresoarele lor au un indicator care arată numai orele de funcționare, nu și orele de mers în sarcină.
Sistemele de comandă bine adaptate pot ajuta prin creșterea factorului de încărcare până la peste 90%, obținând economii de energie de până la 20% sau mai mult.
1. Control intern pentru compresor
a) Comandă de mers în sarcină / gol
Majoritatea compresoarelor au motoare de antrenare trifazice asincrone. Însă, frecvența de pornire permisă a acestora devine mai joasă pe măsură ce motorul este mai mare.
Aceasta nu corespunde frecvenței de pornire necesare pentru a cupla și decupla compresorul cu diferențe mici care să satisfacă cererea efectivă de aer comprimat.
Aceste cicluri doar descarcă zonele presurizate din sistemul compresor. Motorul de antrenare, pe de altă parte, trebuie să continue să funcționeze o anumită perioadă pentru a evita depășirea frecvenței sale de pornire (fig. 1). Puterea necesară pentru a antrena motorul în timpul acestei perioade de mers în gol trebuie privită ca o pierdere.
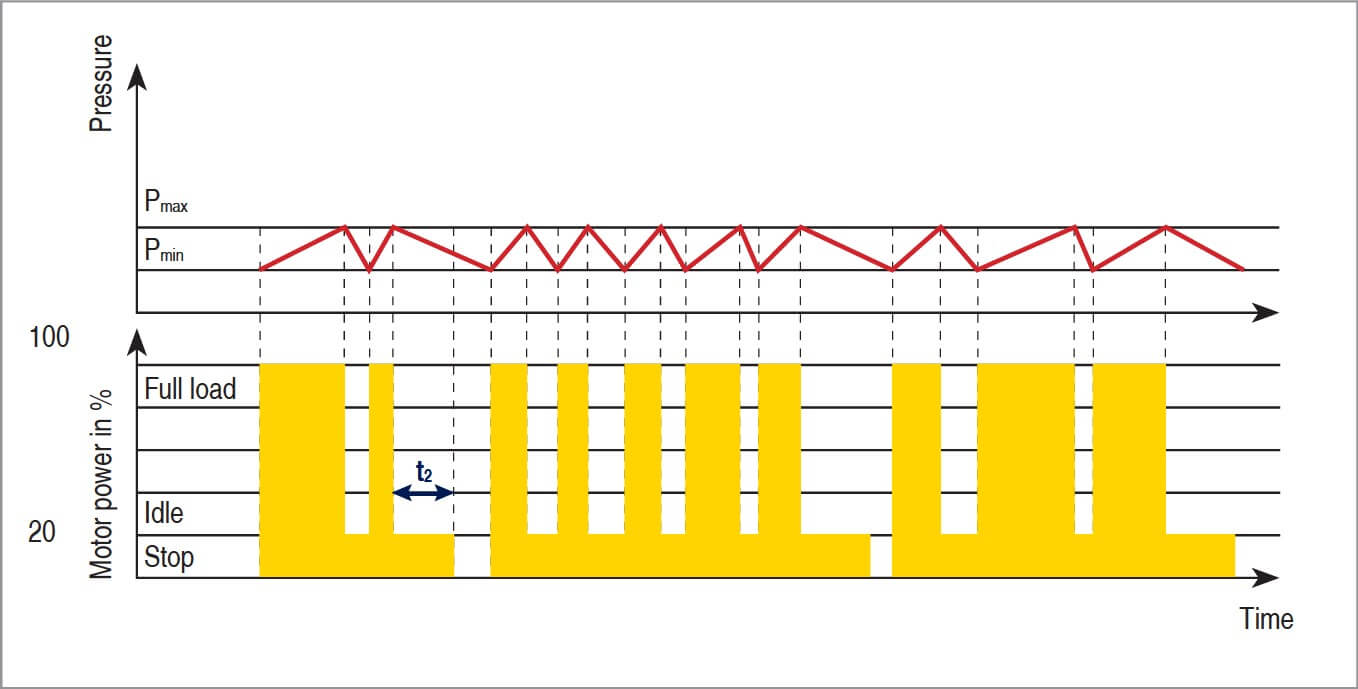
Consumul de energie al unui compresor la mers în gol reprezintă circa 20% din energia necesară funcționării în sarcină.
Sistemele de control moderne, optimizate de calculator, cum ar fi controlul Quadro cu selectarea automata a modului de funcționare optimă (fig. 2), controlul Dynamic cu mers în gol dependent de temperatura motorului (fig. 3) și controlul Vario cu perioade de mers în gol variabile calculate (fig. 4) ajută la menținerea la minim a perioadelor costisitoare de mers în gol și asigură protecția maximă a motorului.
Fig. 2: Control sarcină maximă – mers în gol – pornit/ oprit, cu selectarea automata a modului de funcţi- onare optimă, aşa-numitul control Quadro Fig. 3: Control Dynamic, bazat pe controlul Dual, cu mers în gol dependent de temperatura motorului Fig. 4: Control Vario cu perioade de mers în gol variabile calculate
Controlere proporționale care restricționează admisia nu sunt recomandate, deoarece compresorul necesită circa 90% din energia cu care ar trebui să furnizeze 100% din debitul nominal de aer, pentru a furniza doar 50% din acest debit.
b) Antrenare cu frecvență variabilă
Eficiența compresoarele cu turație controlată de un convertizor de frecvență (fig. 5) nu este constantă în toată gama de control. De exemplu, pentru un motor de 90 kW, în gama de control între 30 și 100%, eficiența se reduce de la 94 până la 86%. La aceasta se adaugă pierderile convertizorului de frecvență și caracteristica de putere neliniară a compresoarelor.
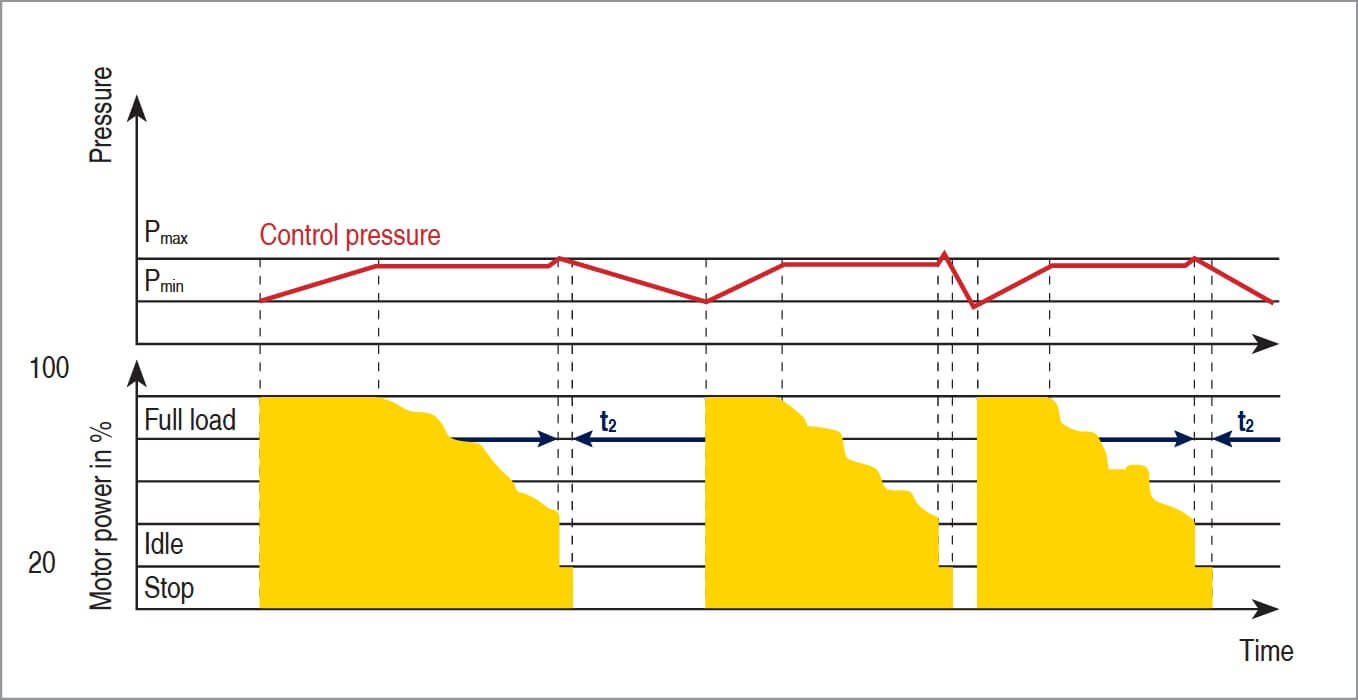
Compresoarele controlate de un convertizor trebuie să fie operate în gama de control 40-70%: acesta este intervalul pentru performanțe optime. De asemenea, toate componentele trebuie proiectate pentru 100% încărcare.
În cazul în care compresoarele cu turație variabilă sunt utilizate necorespunzător pentru o aplicație, acestea se pot transforma în mari consumatoare de energie fără știrea utilizatorului.
Aceasta înseamnă că antrenarea cu frecvență variabilă nu constituie un panaceu universal în ceea ce privește funcționarea eficientă și economică.
2. Clasificarea consumului de aer comprimat
În general, ținând cont de funcția lor, compresoarele pot fi clasificate în unități care preiau sarcina (consumul) de bază, medie și de vârf sau așteaptă în rezervă.
a) Consumul de bază
Consumul de bază este debitul de aer necesar în mod constant pentru o unitate de producție.
b) Consumul de vârf
Prin contrast, consumul de vârf este debitul de aer cerut în momentele de consum maxim. Acesta este variabil datorită variației cererii de la diverși consumatori.
Pentru a răspunde cât mai bine diverselor cerințe de consum, fiecare compresor trebuie să fie controlat individual printr-un controler intern.
Aceste calculatoare industriale trebuie să poată susține funcționarea compresoarelor și, deci, alimentarea cu aer comprimat în cazul apariției unei defecțiuni a controlerului central coordonator ‘master’.
3. Control central pentru compresoare industriale
Controlerele centrale moderne, echipate cu software bazat pe web, sunt capabile atât să coordoneze funcționarea compresorului într-o stație de aer comprimat, pentru a asigura o eficiență energetică optimă, cât și să asigure posibilitatea de a aduna date de performanță și documente doveditoare ale eficienței sistemului de alimentare cu aer comprimat.
a) Repartizarea sarcinii (splitare)
Aceasta presupune împărțirea compresoarelor cu mărimi și tipuri de comandă și control identice sau diferite în funcție de consumurile de aer comprimat de bază și de vârf ale unei unități de producție (fig. 6).
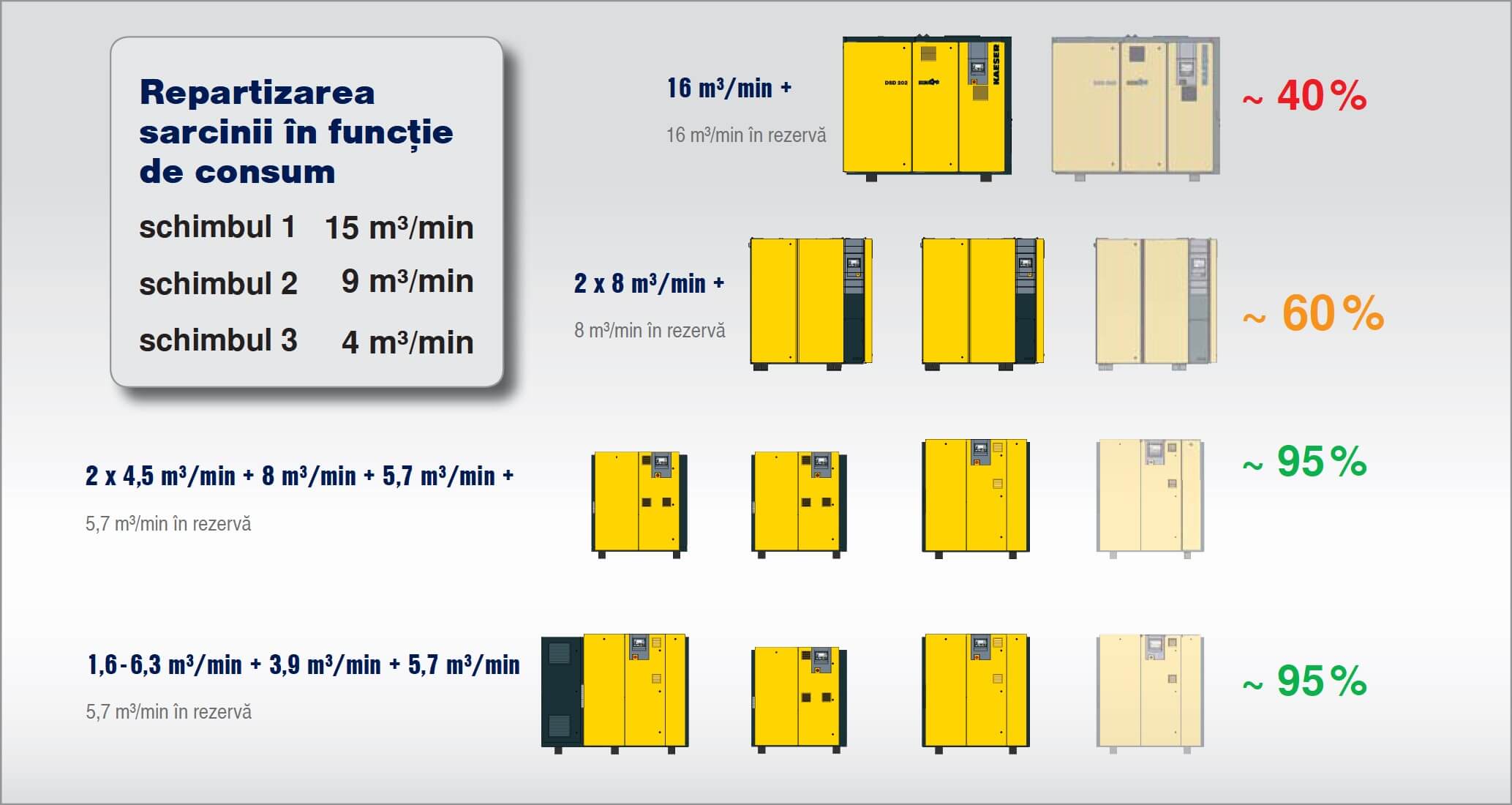
b) Funcțiile controlerului central ale compresoarelor
Coordonarea funcționării unei stații de compresoare este o sarcină dificilă și complexă. Controlerele centrale moderne nu trebuie numai să activeze și în același timp să dezactiveze compresoare de diferite mărci și dimensiuni.
Ele trebuie să fie, de asemenea, capabile să monitorizeze necesarul de întreținere al sistemului, să echilibreze orele de funcționare ale echipamentelor și să înregistreze alarmele pentru a minimiza costurile de service și pentru a maximiza fiabilitatea.
c) Gradarea corectă
Pentru ca un controler central să funcționeze cu eficiență maximă, este necesară gradarea perfectă a compresoarelor din stația de aer comprimat.
Suma debitelor de aer comprimat a compresoarelor de vârf trebuie, deci, să fie mai mare decât debitul compresorului de bază ce urmează a fi cuplat.
Dacă se utilizează un compresor cu convertizor de frecvență, gama de reglaj a acestuia trebuie să fie mai mare decât debitul compresorului de bază ce urmează a fi cuplat, altfel nu poate fi garantată eficiența furnizării aerului comprimat.
d) Siguranța transferului de date
O altă cerință importantă necesară funcționării perfecte și eficienței controlerului central de comandă este siguranța transferului de date.
Trebuie să se asigure transferabilitatea mesajelor între toate compresoarele și între compresoare și controlerul central. În plus, căile de comunicație trebuie monitorizate pentru ca defectele de tipul pierderii continuității la un cablu de conexiune să fie imediat recunoscute.
Metodele de transfer obișnuite sunt:
- Contacte fără potențial
- Semnale analogice 4 – 20 mA
- Interfețe de comunicație, ex.: RS 232, RS 485, Profibus DP sau Ethernet.
Cea mai modernă metodă de transfer este Ethernet. Acest sistem poate transmite volume mari de date într-un timp foarte scurt.
Atunci când este combinat cu sisteme de monitorizare și tehnologii moderne de telecomunicații există și posibilitatea conectării și monitorizării de la distanță. Aceasta înseamnă că nu este obligatorie amplasarea controlerelor centrale în instalația propriu-zisă de aer comprimat (fig. 7).
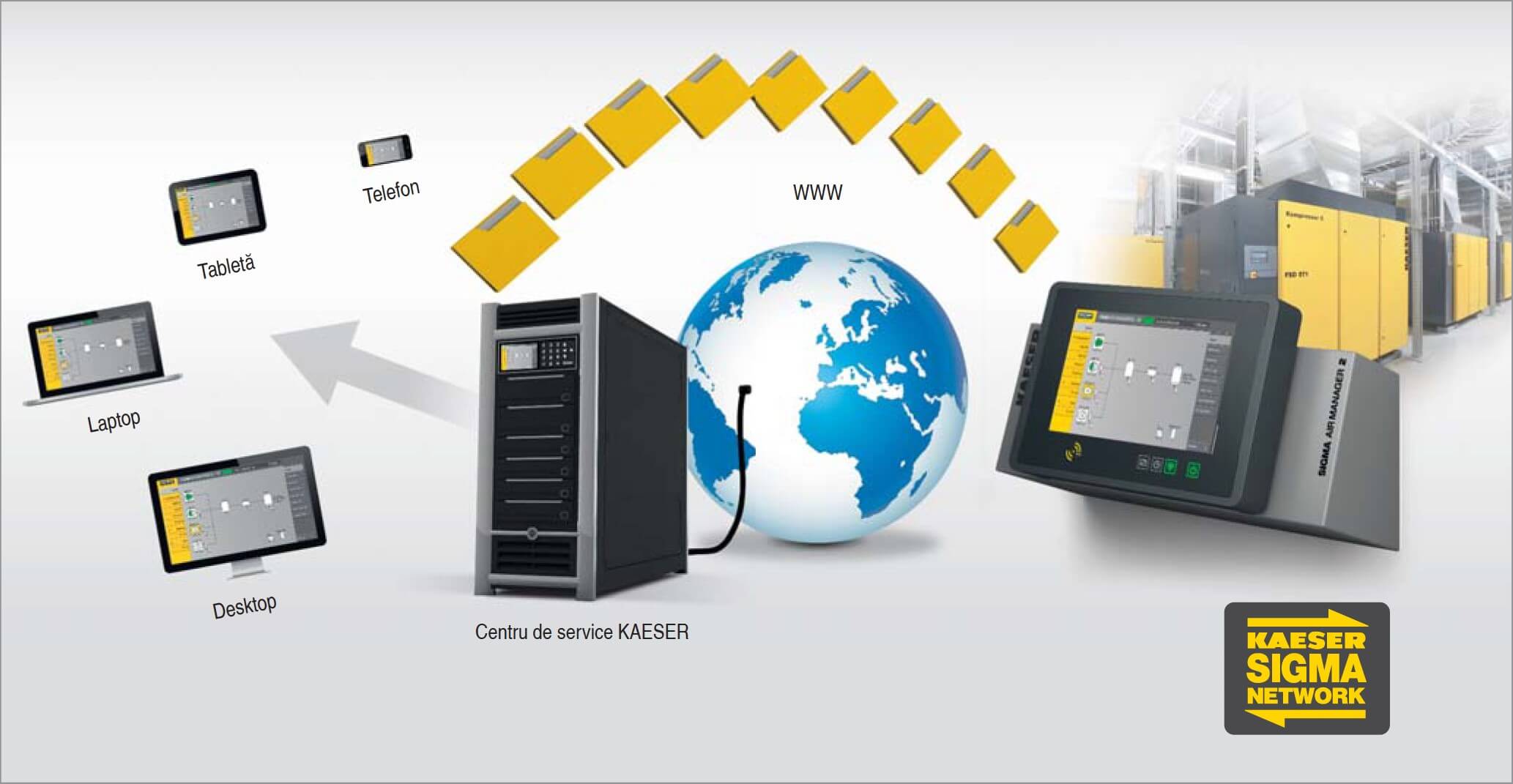