Modern compressed air installations are usually highly complex systems. They are only able to operate at the peak of their performance if this aspect is properly taken into account during all stages of system planning, expansion and modernisation.
KAESER has developed a comprehensive service tool to aid these processes. It combines familiar elements such as compressed air components, customer consultation and advice with modern advances in compressed air engineering information technology. Compressed air is used in more applications than one can possibly imagine.
But the common requirement for the efficient use of compressed air is the reliable production and treatment of compressed air itself. The air system must be able to supply air in the specified quantity and quality and at a fair price.
1. Consultation influences efficiency
An air system is cost effective only if it suits the application for which it is intended and fits the location and the conditions under which it operates.
In other words: the compressors, air treatment equipment and pipe work must be correctly chosen, sized and controlled. Furthermore, there must be adequate ventilation and a means of dealing with accumulating condensate and, if possible, there should be a means of recovering the exhaust heat generated by the compressors..
The “KAESER Energy Saving System” (KESS) covers all of these aspects and more as it comprises air demand analysis, planning (fig. 1), implementation, further training and exceptional customer service..
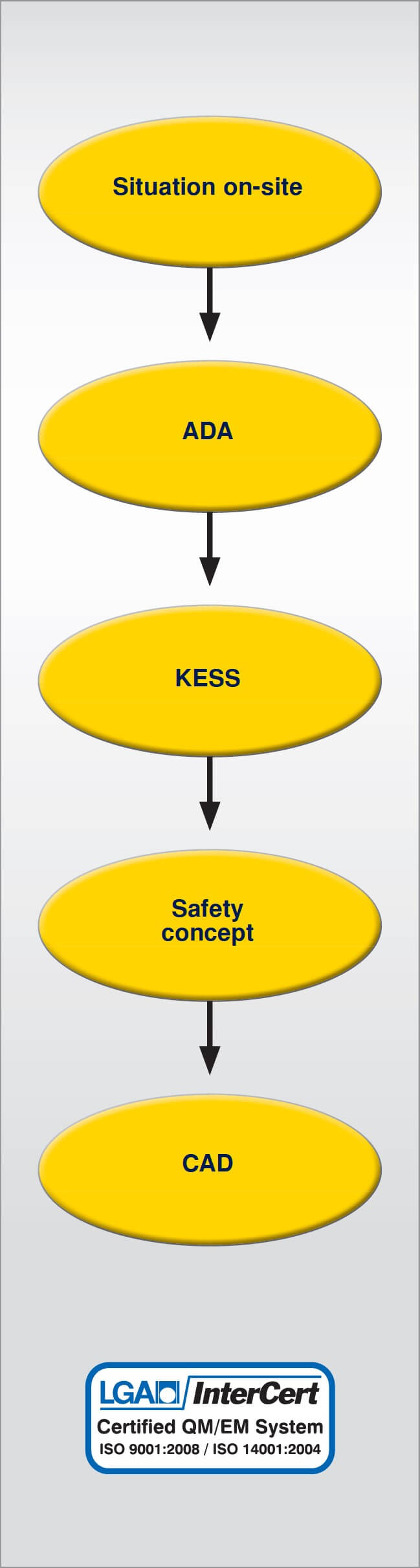
The deciding factors are the quality of the consultation and selection of the correct technology, since the greatest potential for cost savings with any compressed air system lies in efficient power consumption and minimal main- tenance requirement rather than in the initial purchase price.
2. Air Demand Analysis
Detailed investigation into the user’s current and possible future compressed air requirements form the basis of every KESS analysis. This computer-aided process, developed by KAESER and called ADA (Air Demand Analysis), has to take the spe- cific circumstances of the application into account:
a) Designing a new air supply system
When planning a new compressed air supply system, the future operator is first given a special design questionnaire (fig. 2). A KAESER consultant can then interpret the provided information to determine what system equipment would be required in order to best meet the needs of the specific compressed air application.
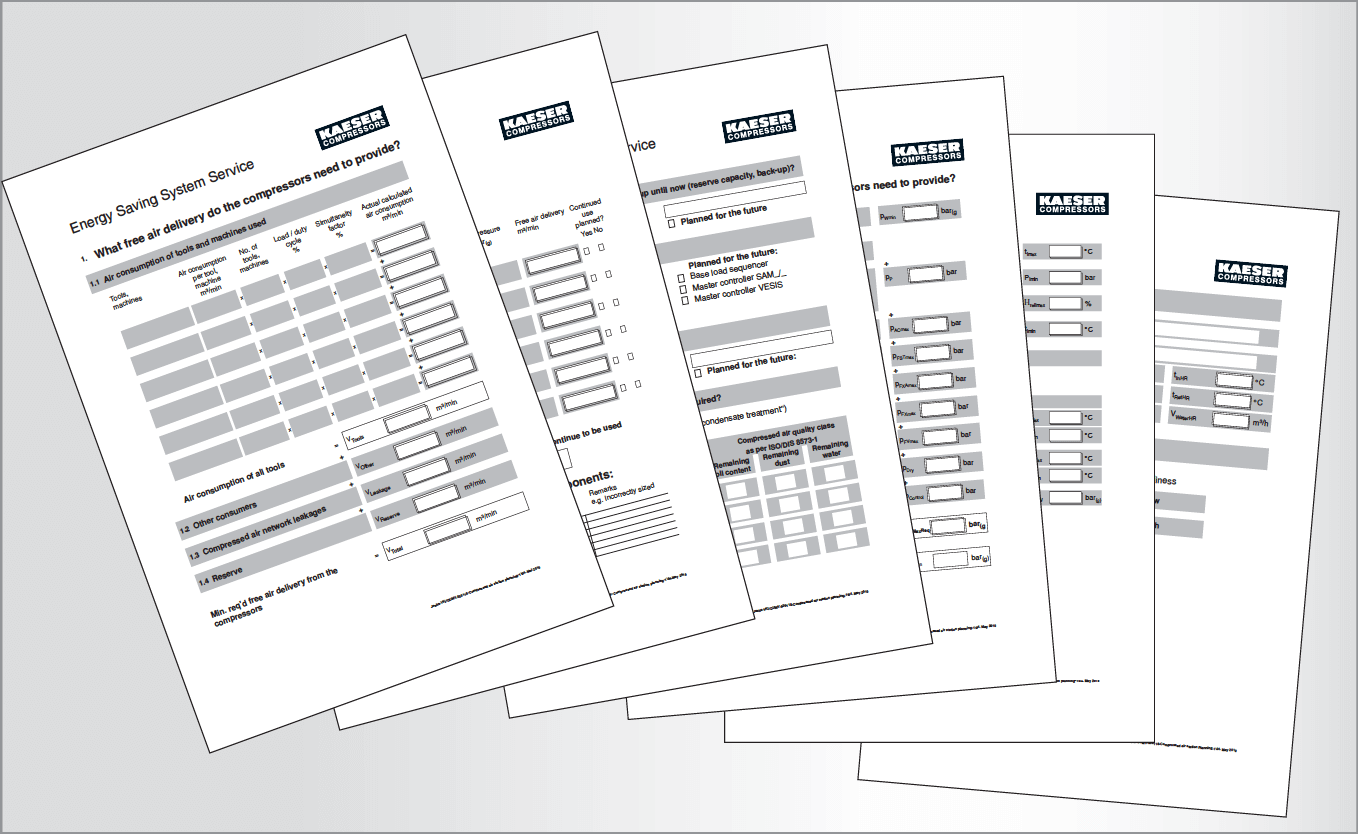
The questions cover every aspect of what comprises an efficient and environmentally-friendly compressed air supply system.
b) Expansion and modernisation
In contrast to new projects, expansion or modernisation programmes involving existing systems usually provide sufficient reference points for new application-tailored design solutions.
KAESER provides measuring instruments and data loggers with which the air demand is precisely determined in various locations and at different times. It is particularly important to determine maximum and minimum as well as average values (fig. 8).
c) Testing the efficiency of an existing air system
It is recommended that the efficiency of an existing air system is checked from time to time with the help of a computer-aided analysis method that determines whether the compressors are (still) correctly loaded, whether the control systems are (still) correctly programmed and whether leakage rates are still within an acceptable tolerance range.
ADA ar trebui utilizată și dacă compresoarele trebuie înlocuite cu unele noi. Astfel se vor evita eventualele erori în ceea ce privește alegerea mărimii compresoarelor care pot determina cicluri de funcționare ineficiente și se va putea alege un sistem central de comandă adecvat.
d) Changes in operating conditions
It is well worth consulting a specialist when the conditions under which an air system operates change. Often simple changes to air treatment methods or pressure matching can be made to suit the new circumstances, achieving sig- nificant cost savings.
3. Operator information
a) Layout plan
A layout plan of the production facility should be available for general orientation (fig. 3).
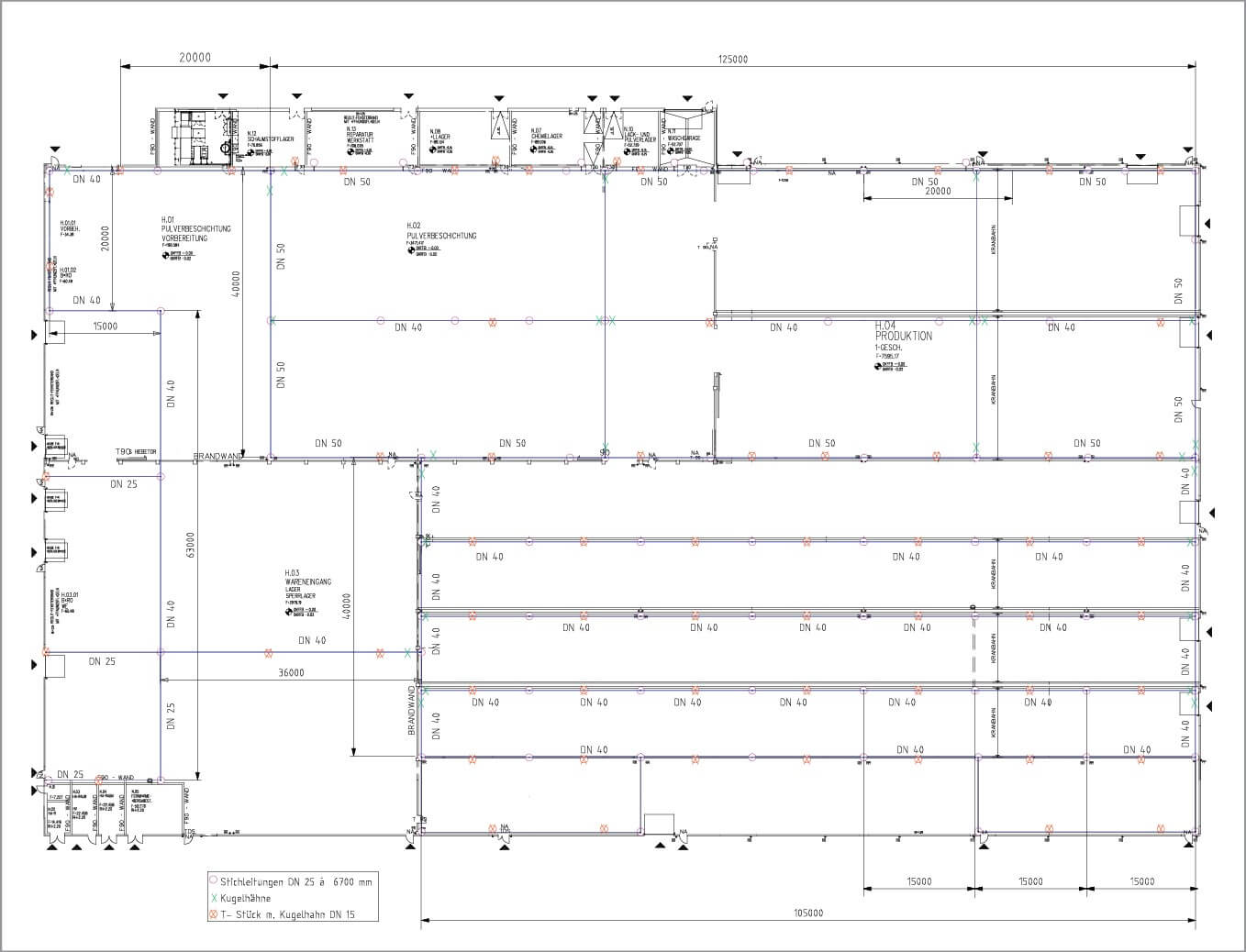
It should show the compressed air station’s compressed air main, connection lines and feeder line connections. Details of pipe diameters and materials, the main air take-off points and any take-off points for air at special pressures and qualities must also be shown.
b) Compressed air applications
As compressed air is a highly versatile medium, it is essential for the user to provide exact details regarding the specific air application: Given information should include, for example, whether the air is to be used as control air, for surface treatment, for rotating tools, for cleaning or as process air, etc.
c) Installed compressors
As well as model and type, the compressors’ technical data – such as working pressure, free air delivery, power consumption, type of cooling and use of heat recovery – should also be mentioned.
d) Compressed air treatment
În ceea ce privește tratarea aerului comprimat, este important să se cunoască dacă acest lucru se face la nivel central sau local și ce clase de calitate sunt necesare. Evident, trebuie specificate datele tehnice ale componentelor iar o schemă de curgere va oferi privirea de ansamblu (fig. 4).
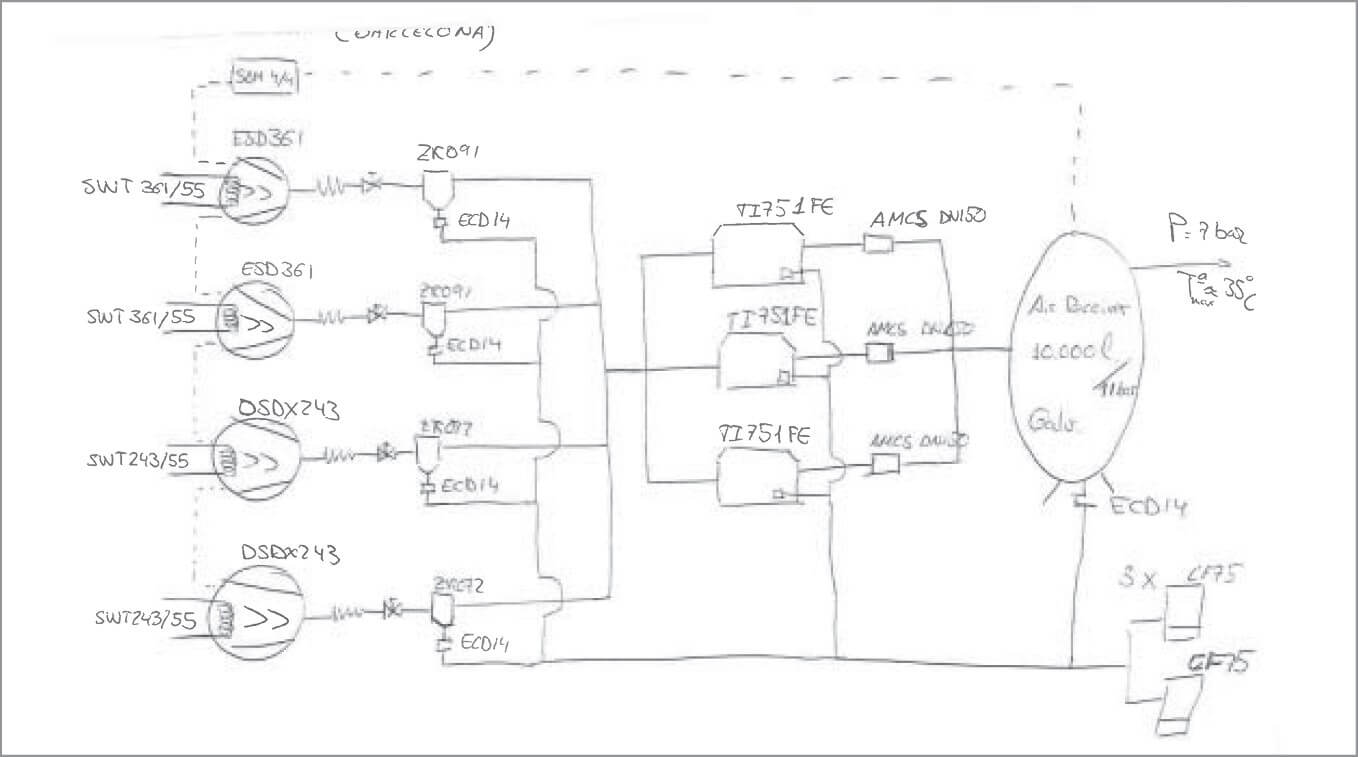
e) Compressor control and monitoring
As the efficiency of a compressed air system is significantly affected by the characteristics both of the individual compressors and they way they interact with one another, it is also important to include details regarding the control and monitoring systems that are used.
4. Discussions between the user and specialist
Once the above information is made available, the compressed air specialist should be familiarised with the relevant documents and then a discussion should follow detailing any issues with the air supply. Such issues might include: low or fluctuating pressure, poor air quality, inadequate utilisation of compressors or problems with cooling.
5. Inspection
Etapa cea mai importantă o constituie inspecția sistemului de aer comprimat. Aceasta trebuie să înceapă întotdeauna din zona cea mai critică, adică acolo unde se așteaptă cea mai mare cădere de presiune (fig. 5). Experiența arată că acestea sunt adesea punctele finale de racordare.
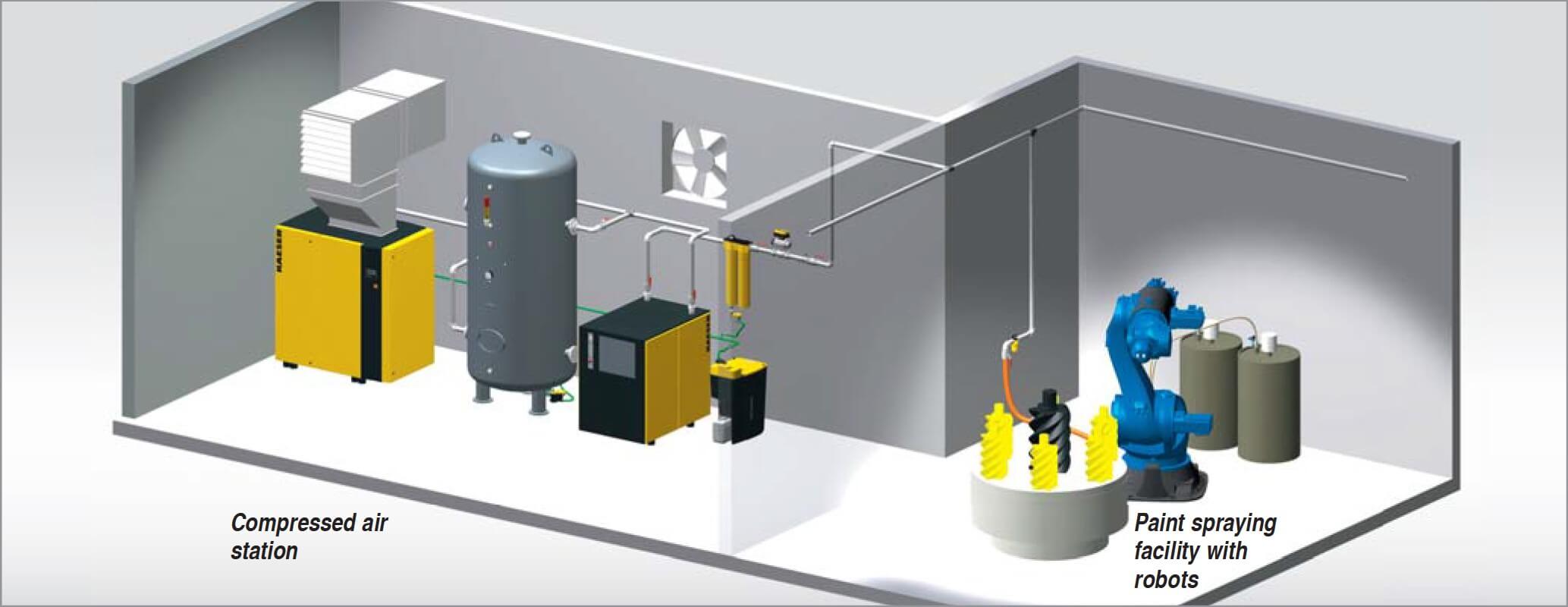
a) Connection hoses, pressure regulators, water separators
The hose connections to the air consuming equipment are highly susceptible to leaks. These should be thoroughly checked. If pressure regulators are installed then their pressure settings (inlet and outlet pressure) should be checked under load (fig. 6).
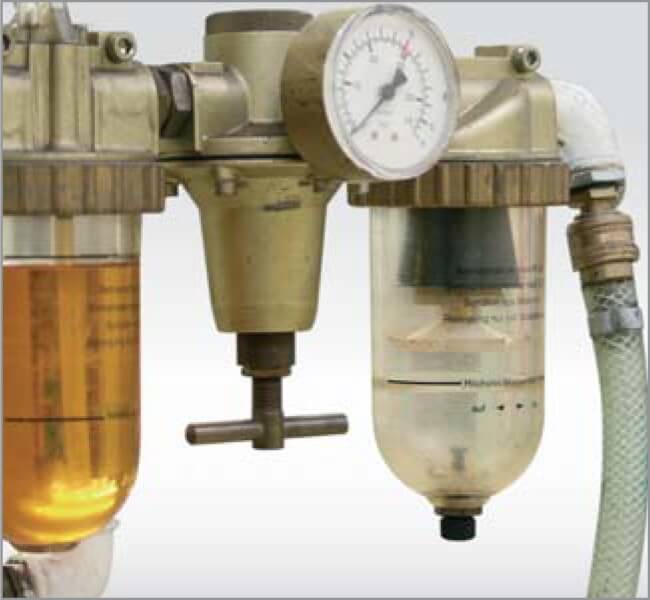
Water separators installed upstream from pressure regulators should be checked for fluid accumulation and contaminant build-up. The same applies to drainage pipes that lead straight down (fig. 7).
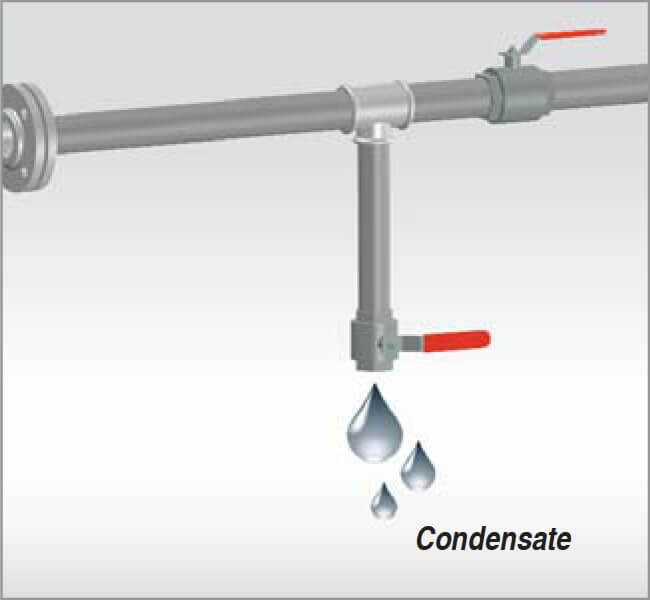
b) Shut-off valves
Distribution lines and their fittings leading away from the main line significantly affect system efficiency. Shut-off valves and similar equipment also play an important role: they should be adequately sized, full-flow ball or butterfly types, not inefficient water taps or angle valves.
c) Main ring
The most important point is to detect causes of pressure drops such as narrowed sections.
d) Compressed air treatment system
The most important inspection criteria here are the pressure dew point achieved (degree of dryness) and the pressure drop across each component. Further quality checks may be required depending on the application.
e) Compressed air station
Of course the compressed air station itself may have its own shortcomings. In particular, the location of the compressors, ventilation, cooling and pipework should be checked. Furthermore, the cumulative pressure swing of the compressors, the size of the air receiver and the location of the pressure measurement points from which the compressors are controlled must be checked.
f) Determining ADA measurement points
When the inspection is completed, the specialist and the user decide on the points at which the measurements are to be taken. The minimum requirement is to measure points upstream and downstream of the air treatment system and at the outlet of the compressed air distribution network.
6. Measurement of pressure and air consumption (ADA)
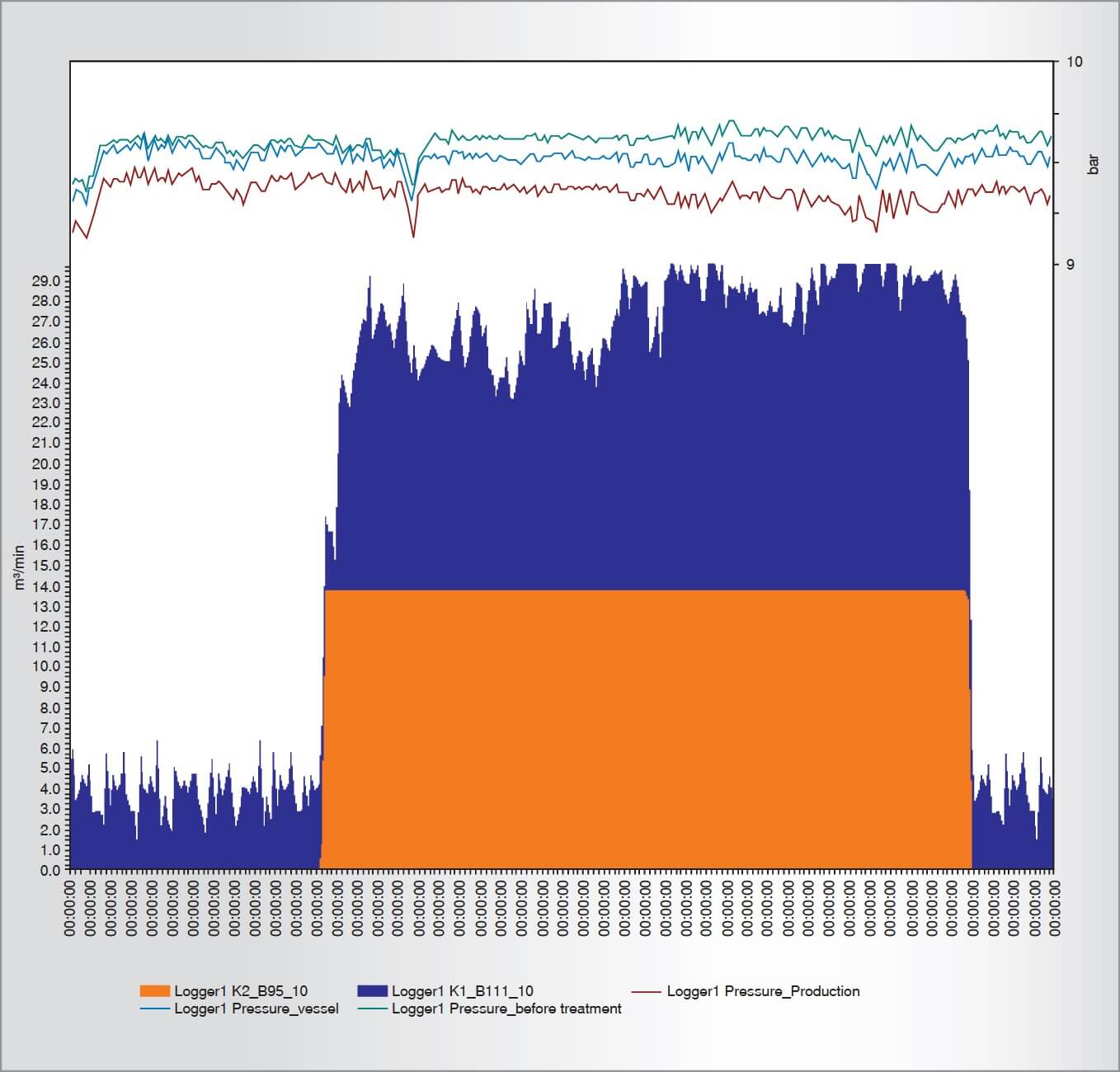
During measurement of pressure and air consumption, the operation of the compressed air system is monitored over a period of at least 10 days with the help of advanced data logger technology. The data logger collects all relevant information and transfers it to a PC which uses this data to create an air demand profile. relationship of individual compressor performance to respective air consumption.
The graph shows pressure drops, fluctuations in pressure and consumption, off-load profiles, on-load and standstill periods of the compressors and the relationship of individual compressor performance to respective air consumption. In order to complete the picture, the leaks also have to be determined during this measurement process.