Strategic planning that takes into account the energy consumption and the costs of air compressors, however, only half of the problem. In the long run, only the efficient operation of the compressor system ensures the reliable production of compressed air.
Maximum compressed air efficiency brings triple savings: air system reliability increases, whilst compressed air costs and power consumption significantly decrease
The efficiency potential is impressive to say the least: The EU „SAVE II” EU study showed the extent of the potential savings that can be achieved: Compressors in the EU consumed 80 billion kWh in 2000. At least 30 percent of this energy could be saved (Fig. 1).
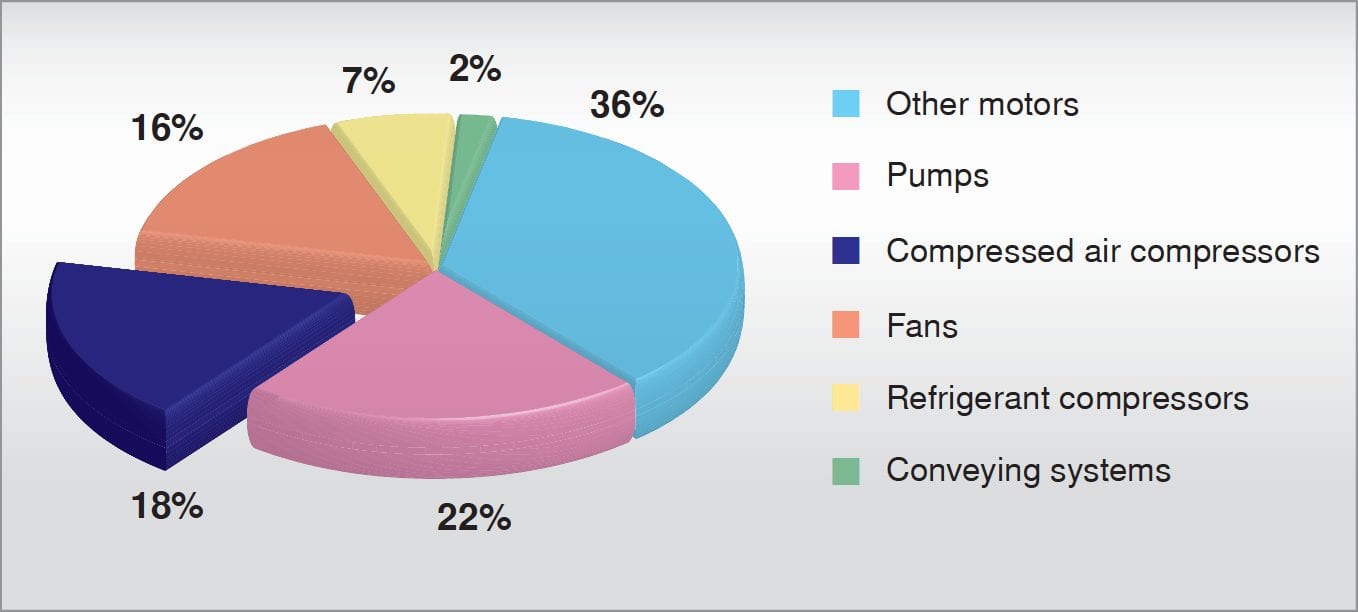
1. What is “optimum efficiency” for industrial air compressor?
The efficiency of a compressed air system is reflected by its cost structure.The achievable optimum is never the same because it is related to a specific company and its production. Critical factors are compressor operating life, working pressure and other commercial parameters.
The example illustrated is an optimised system with air-cooled compressors, operational life 5 years, power costs 8cent/kWh, interest rate 6% , 7b ar working pressure, air quality to ISO 8573-1: Class 1 residual oil content, Class 1 remaining dust content, Class 4 remaining water content. The example shows that even under optimum conditions power consumption still takes up the lion’s share of overall compressed air costs (around 70% ) (fig. 2).
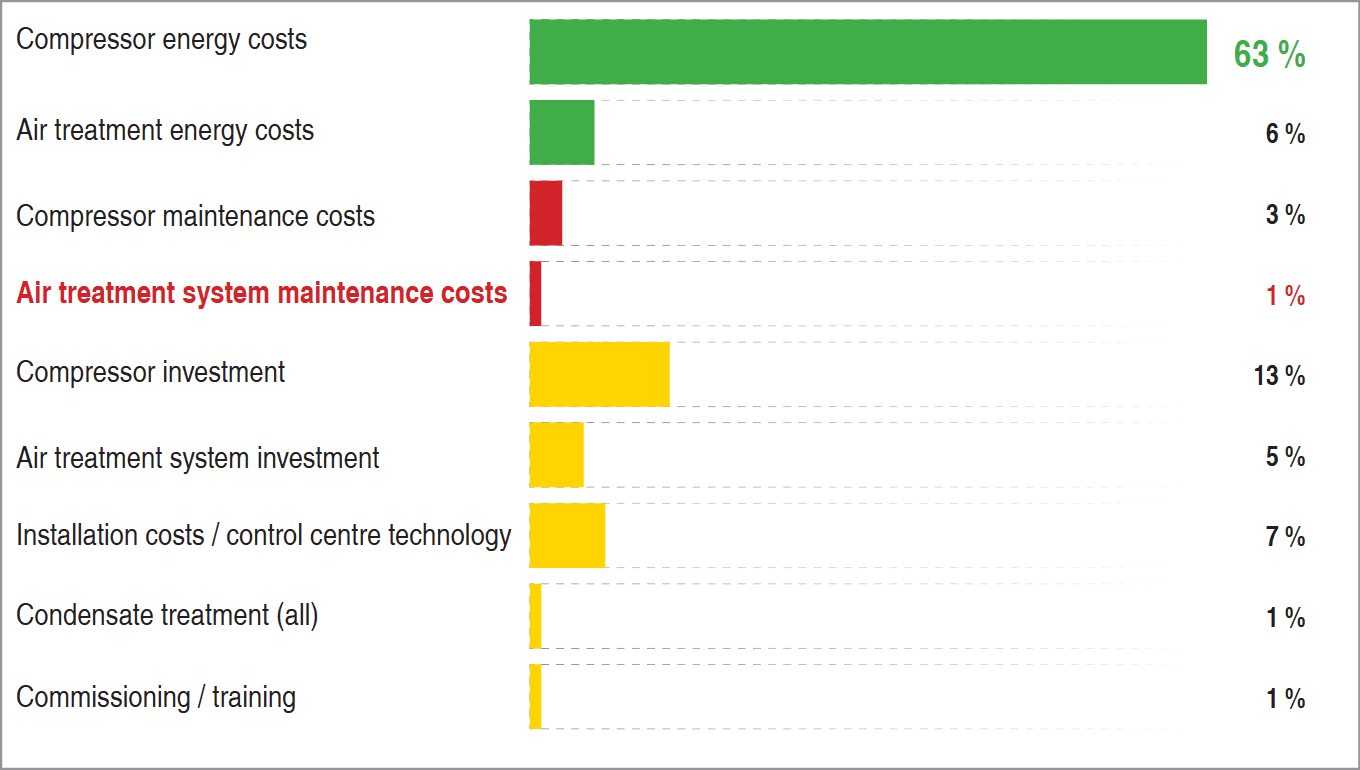
A University of Coburg study in 2003 (fig. 3) highlighted the inefficiencies of compressed air stations in use in Germany.
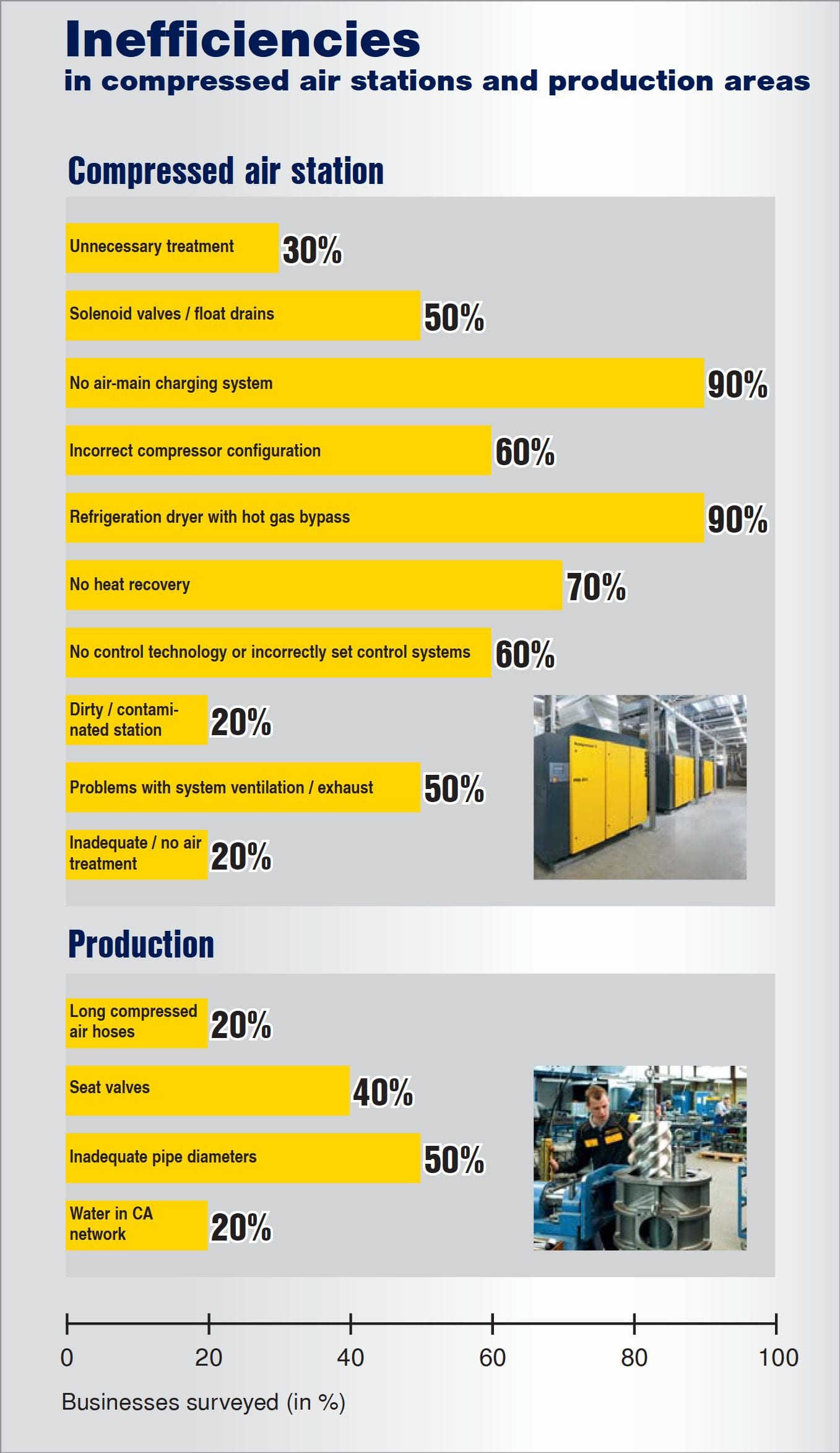
2. Maintaining efficiency
Anyone interested in long-term compressed air system efficiency should consider the following points carefully:
2.1 Demand-oriented maintenance
Advanced internal compressor controllers such as the SIGMA CONTROL, and compressed air management systems, such as the PC-based SIGMA AIR MANAGER 4.0, provide detailed service interval information for the components that comprise the compressed air station. This has made it possible to carry out preventive maintenance and demand-oriented service work. This results in lower maintenance costs, as well as increased efficiency and reliability.
2.2 Matching air-consuming equipment
It is only too easy to make ‘savings’ for compressed air production and consumption in the wrong places, e.g. to use a budget-priced production machine that requires a higher working pressure. The cost of generating pres- sure higher than the standard 6 bar, for example, would quickly rise above the extra cost for a more efficient machine working with a lower pressure.
Therefore, when considering the specification of new air-consuming production machines, the pressure of the air needed is just as important as the electrical power supply, which is why guidelines should be written for the purchase of such production machines that cover both electrical power and compressed air supplies.
2.3 New production-related requirements
2.3.1 Compressed air consumption
a) Changes to production of air compressors
In most manufacturing facilities the compressed air demand varies from shift to shift. However, if not taken into consideration, changes to a production process may result in compressors operating far below capacity in one shift, yet in others not being able to cover demand – even with reserve capacity. The air supply should therefore be designed to accommodate any such changes. As a result, the design of the compressed air system is made to adapt to any such changes.
b) Expansion in production of air compressors
In this case not only the compressor capacity but also the pipe work and the air treatment equipment may have to be adapted to meet the increased demand. It is advisable to precisely measure and document the air consumption of the existing compressor system in order to gather enough detailed information to economically modify or expand the air supply system to produce the higher capacity needed.
2.3.2 Air supply reliability
It is usual to include a standby compressor in an air station to provide coverage when another is being ser- viced or replaced and to cater for occasional demand peaks. Such a reserve capacity, however, should be matched by reserve capacity in the air treatment equipment.
When air consumption rises, the standby compressor cuts in, but because of the lack of additional air treatment capacity the compressed air quality deteriorates as a result. Therefore, a treatment unit (dryer/filter) should be provided for each standby compressor.
2.3.3 Changing of air quality
If higher air quality is needed the procedure differs depending on whether all areas of production are affected or only one specific area. In the former case, it is not enough to simply re-equip the central compressed air supply. The pipe work that has transported air of lower quality will have to be cleaned or renewed.
In the latter case, local air treatment that can supply the quality required is recommended. Airflow through local treatment devices should be limited. This ensures that an increase in demand above that for which the devices are intended does not result in degradation of air quality.
2.4 Monitoring leaks of compressed air systems
Leakages occur in every compressed air distribution network and can lead to considerable energy losses. The main cause is wear on tool, hose connections and machine components (Fig. 4).
This is why it is vital to keep track of such problems and to take prompt action whenever they occur. It is advisable to regularly measure overall leakage with the aid of modern control and monitoring systems such as the SIGMA AIR MANAGER. If an increase is recorded, the leaks must be traced and eliminated.
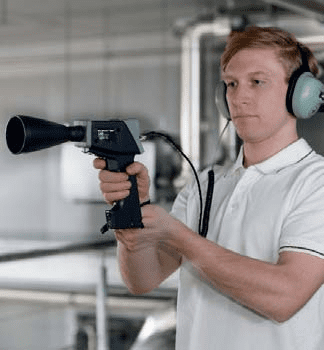
3. Cost management ensures efficiency
Information gathered through analysis during the planning stage is also relevant for future system operation. Once the system is installed and running, however, no special analysis is needed to acquire data at a later stage.
These tasks are taken over by advanced master controllers such as the SIGMA AIR MANAGER.
This forms the basis for comprehensive compressed air audits and effective compressed air system cost-management (Fig. 5a to e).
The more users introduce transparency into their air cost structure, search out potential savings and give priority to energy efficiency rather than price when purchasing air supply equipment, the nearer we will get to achieving the calculated 30 percent energy-saving potential.
That’s not only good for the balance sheet, but also benefits the environment.
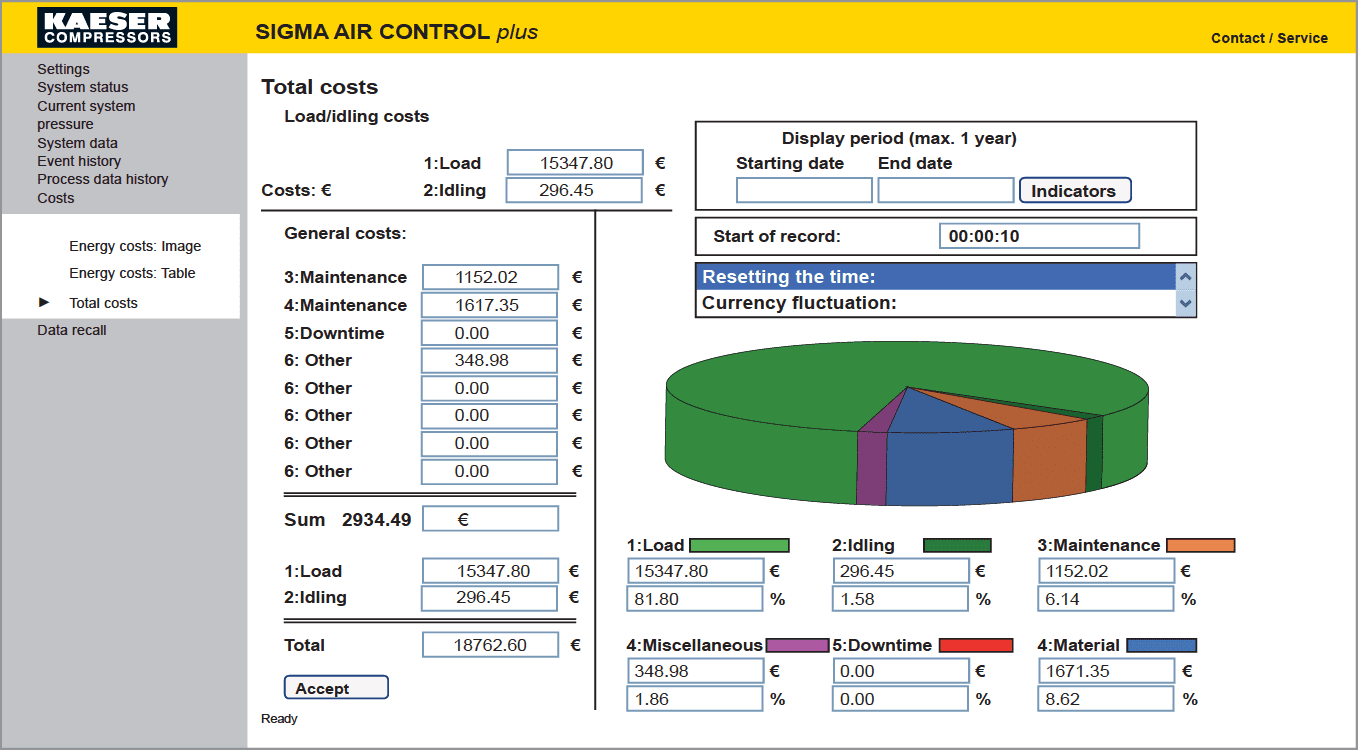
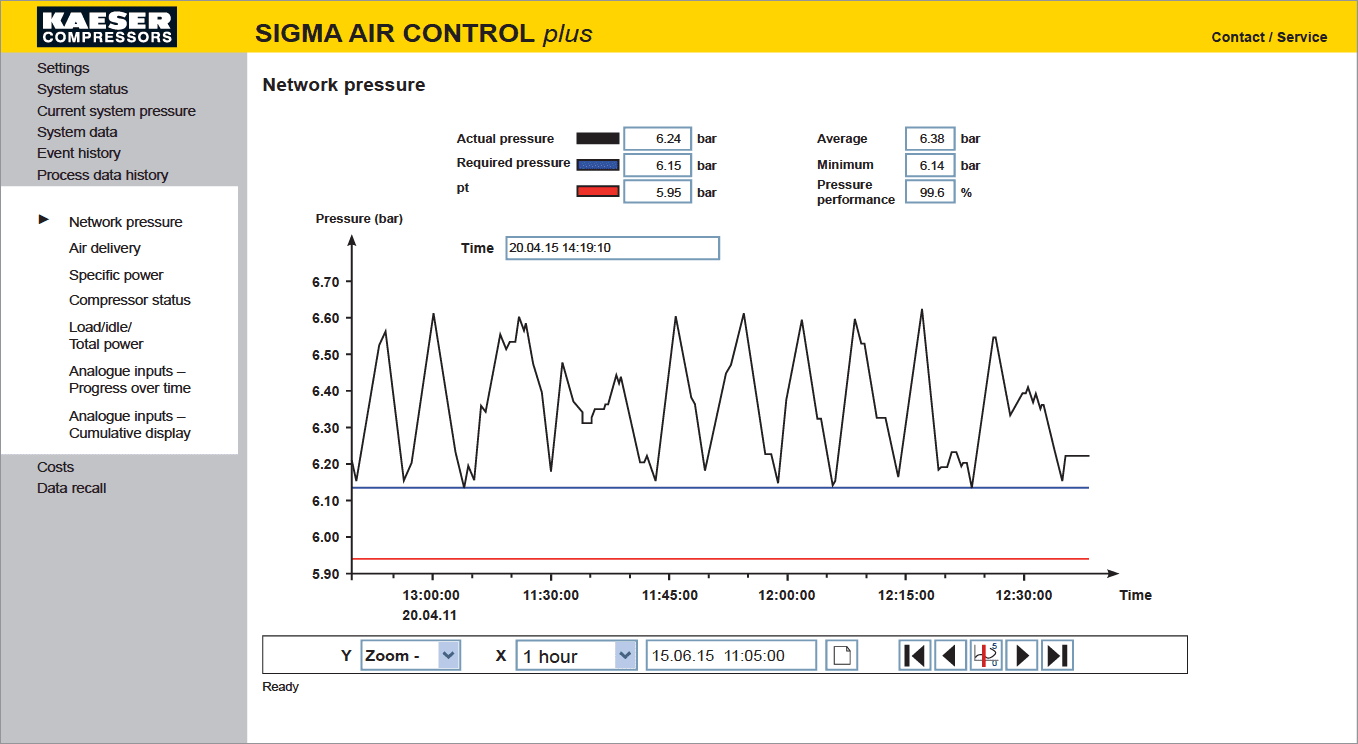
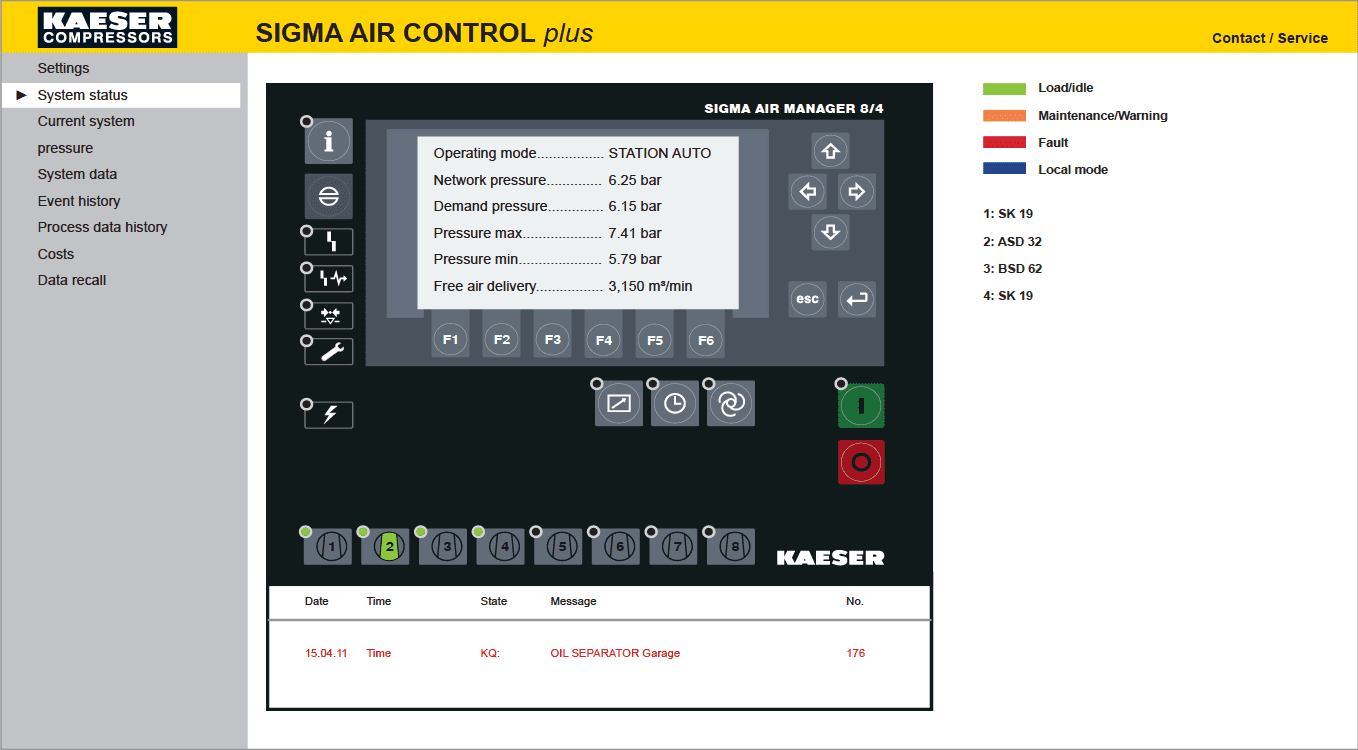
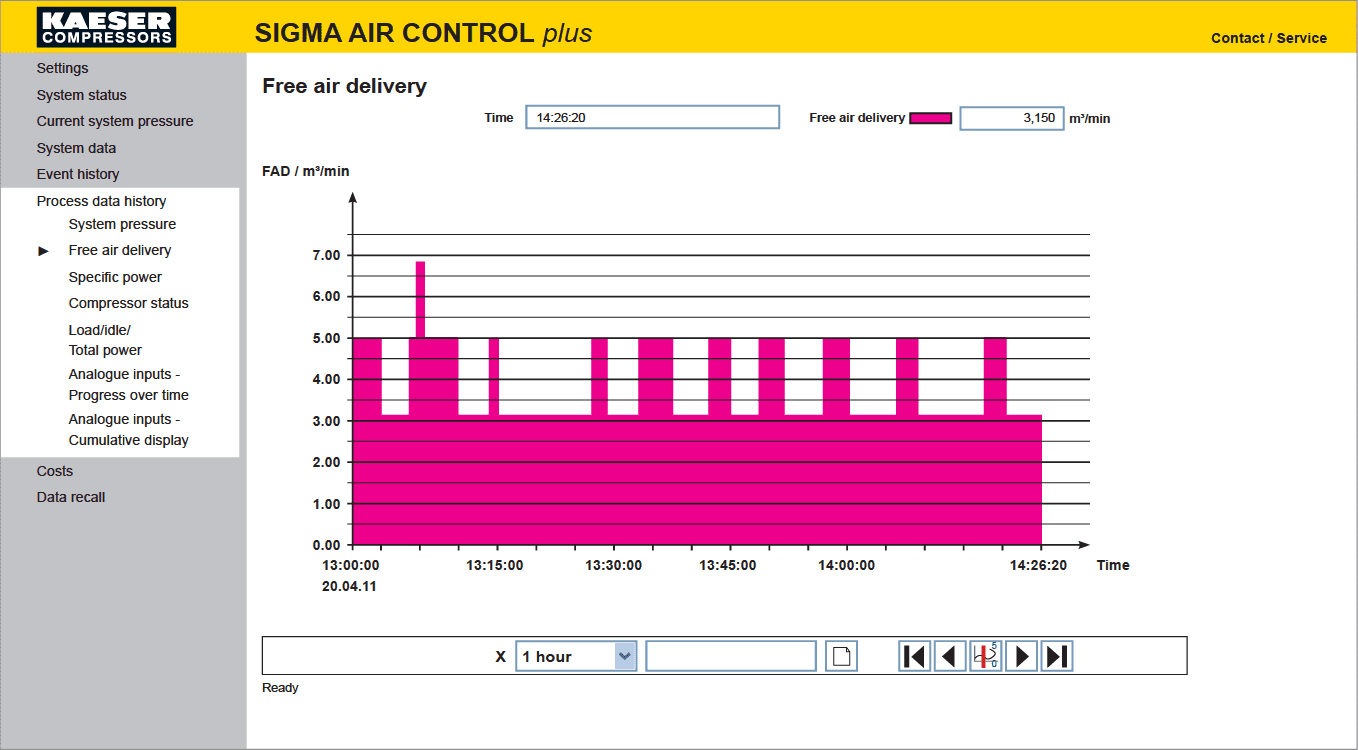
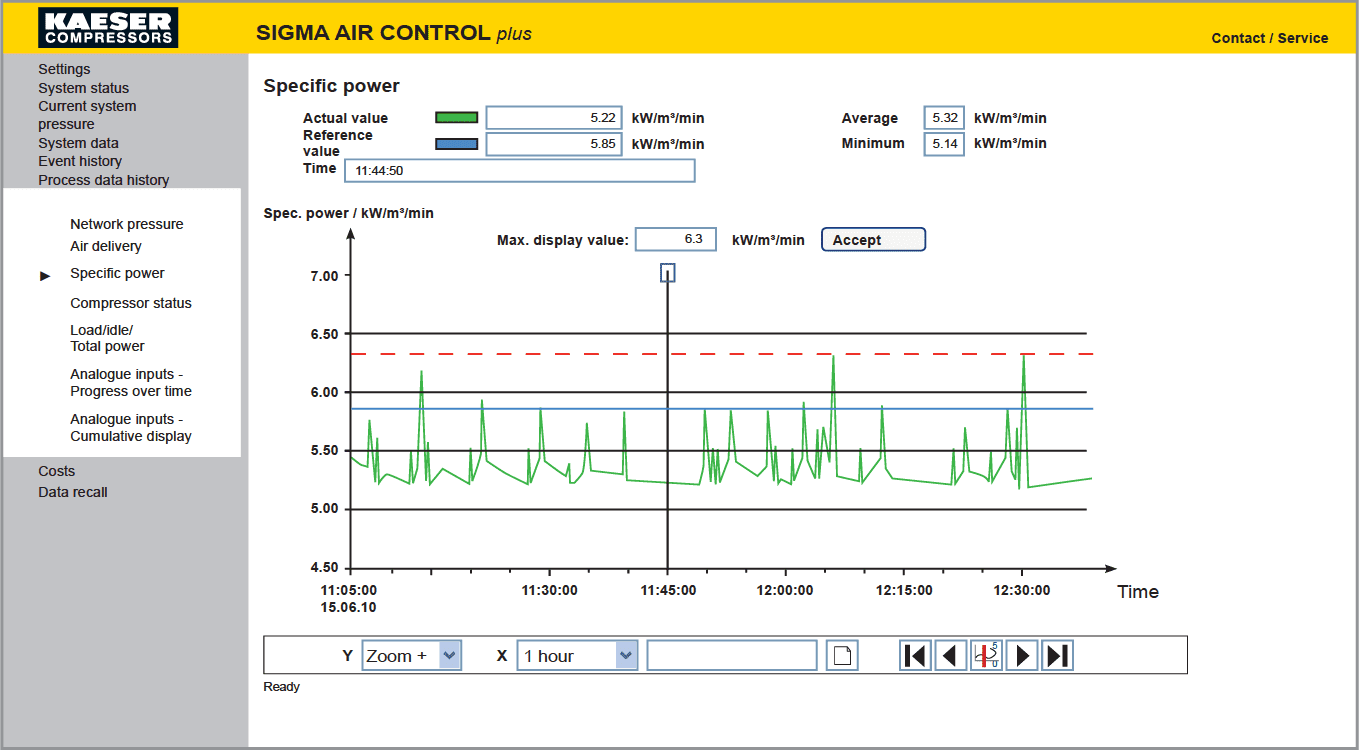