The compressor station pressure is actually correct, but pressure is too low at the air-consuming equipment. What’s the cause?
In this case, hoses, quick couplings and pressure regulators are commonly the offending components. But often the pressure at the take-off point in the system is too low: for example, of the 6.8 to 7bar originally available for the tools, a mere 5 bar remains.
Operators often turn to a quick fi x: “Let’s just set the station pressure 1 bar higher, who cares!” But this is problematic, because for every pressure increase of 1 bar, the energy consumption of the compressor station increases by 6% – and the leakage rate also sharply increases.
It’s therefore advisable to identify the causes and implement an appropriate solution.
Pipe network as the source of the problem
When the pressure directly downstream of the compressor is correct and there is no disproportionately large reduction due to downstream treatment components, the problem can only be in the pipe network.
This is divided into three sections: the main line, distribution line and connection line (fig.1). In an optimised compressed air system , the following pressure drops are reasonable from an efficiency perspective:
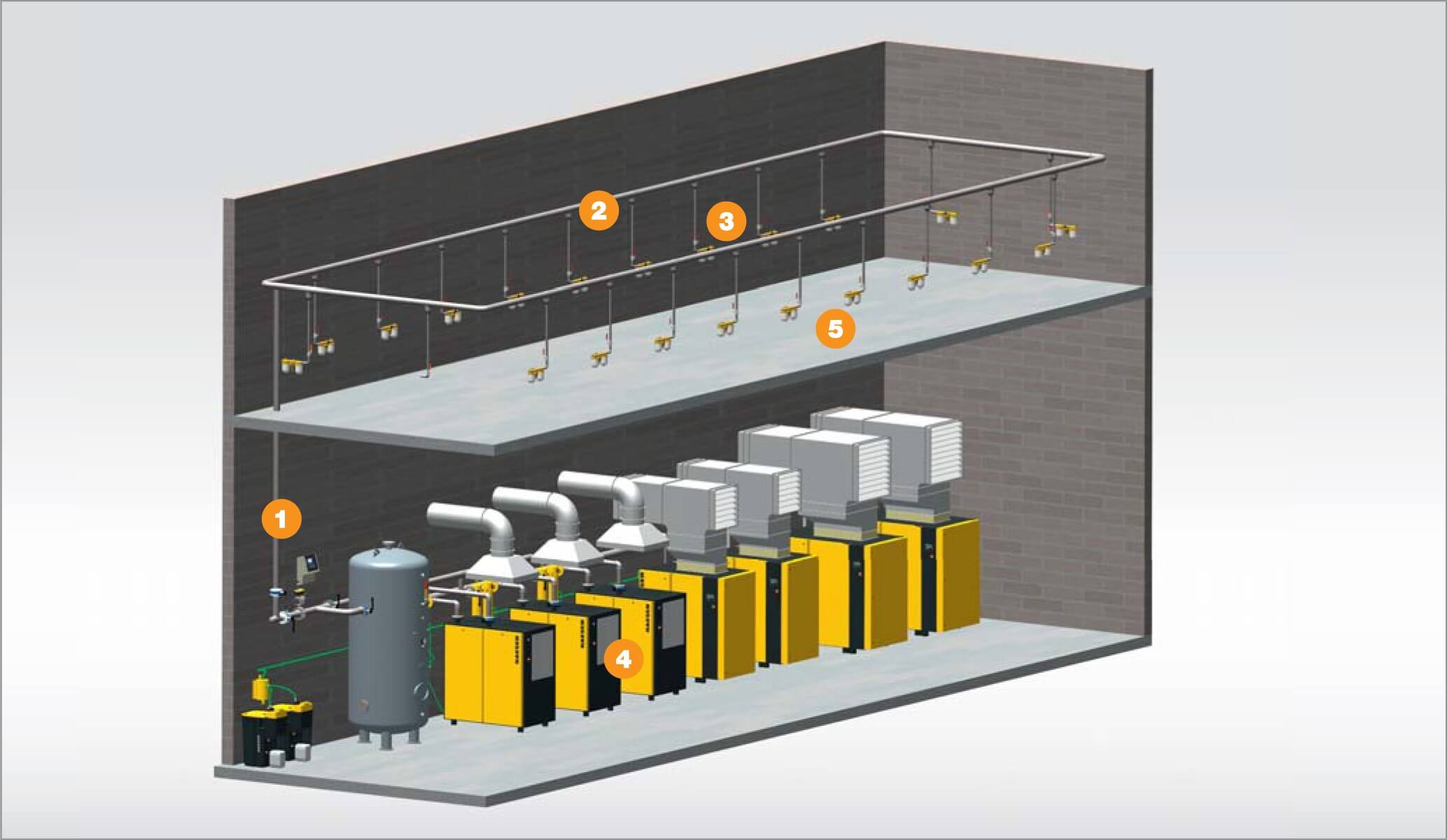
Eliminate ‘bottlenecks’
Upon closer inspection, it often becomes apparent that although the main line and distribution lines have the correct dimensions, the connection lines are too narrow.
For these, the pipe width should not be less than DN 25 (1”). For precise determination of the cross-section, KAESER KOMPRESSOREN offers a convenient on-line tool.
Ensure correct connections
Pentru a preveni întreruperile și daunele cauzate de eventualele acumulări de condens, conexiunile între conductele de distribuție și de conectare trebuie concepute sub formă de „gât de lebădă” (fig. 2): conductele descendente direct pot fi utilizate numai în cazul în care posibilitatea formării condensului în conducte este 100% exclusă (fig. 3).
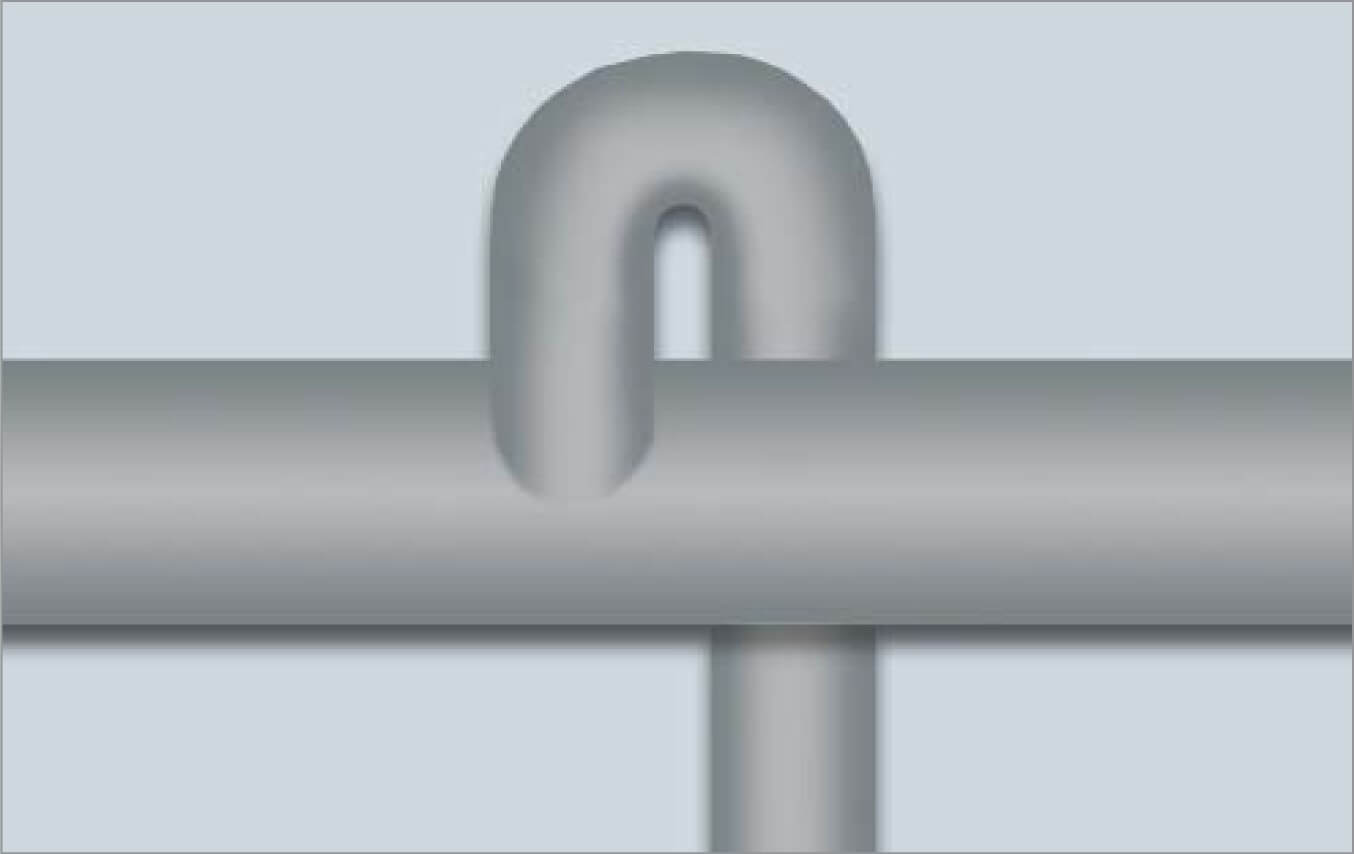
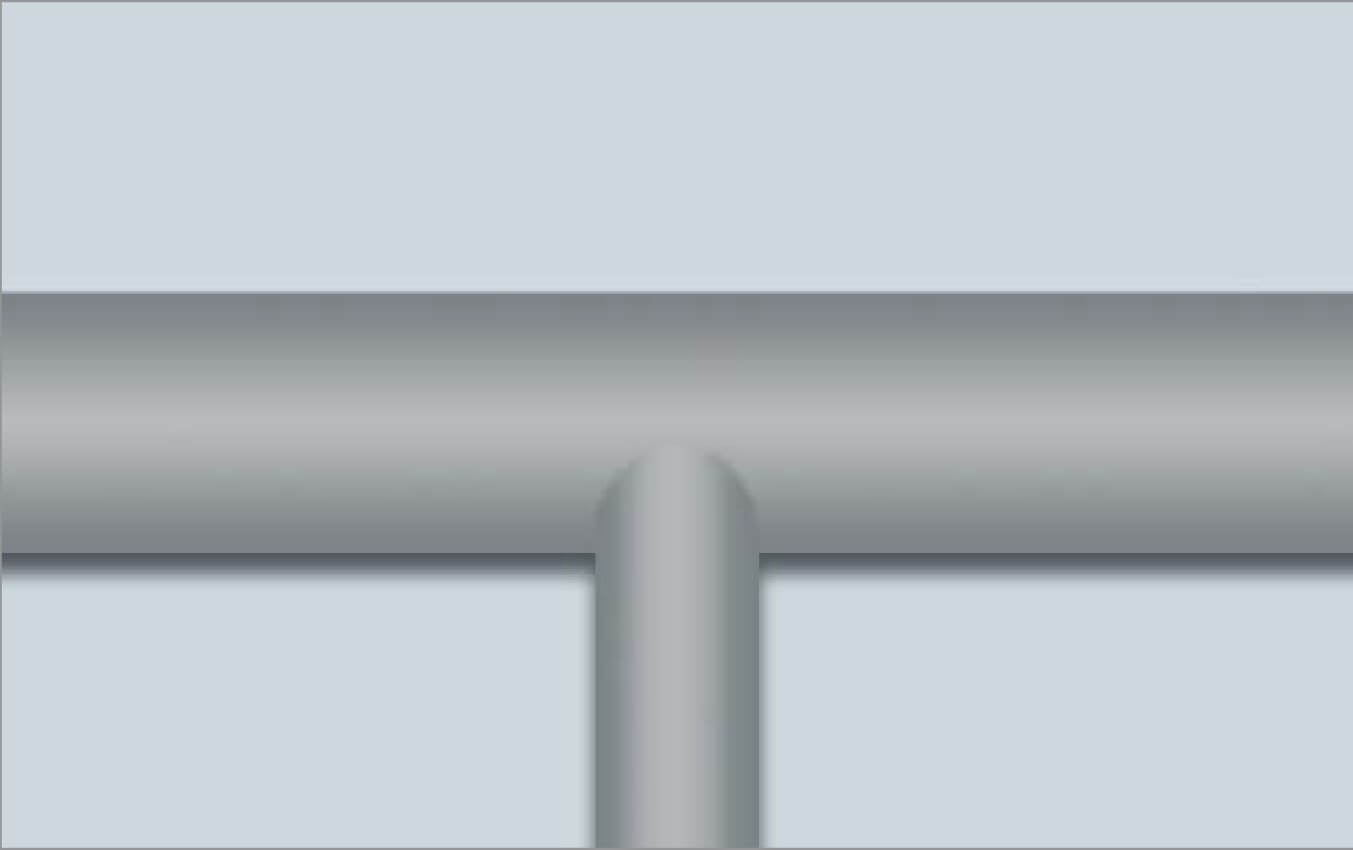