The term ‘condensate’ is misleading because it could be misunderstood to mean only condensed water vapour. Be careful! Every compressor works just like an oversized vacuum cleaner: it draws in contaminated air from the surroundings and passes it on in a concentrated form in the untreated compressed air to the condensate.
1. Why is condensate removed from compressed air?
Users who dispose of condensate by simply pouring it down the drain risk heavy fines. Why? Because condensate accumulating during the production of compressed air is a highly noxious mixture. In addition to solid particles, condensate contains hydrocarbons, sulphur dioxide, copper, lead, iron and other substances caused by increased environmental pollution. That's why legally compliant methods of treating compressed air must be developed.
In Germany, regulations concerning condensate disposal are set out in the Water Management Act. This act stipulates that polluted water must be treated according to the “generally recognised engineering regulations”. This affects all types of condensate – including condensate from “oil-free” industrial compressors.
There are legal limits for all pollutants and for pH-values. These vary according to federal state and the branch of engineering involved. The maximum permissible limit for hydro- carbons, for example, is 20 mg/l and the pH limit for disposable condensate ranges from 6 to 9.
2. Composition of condensate
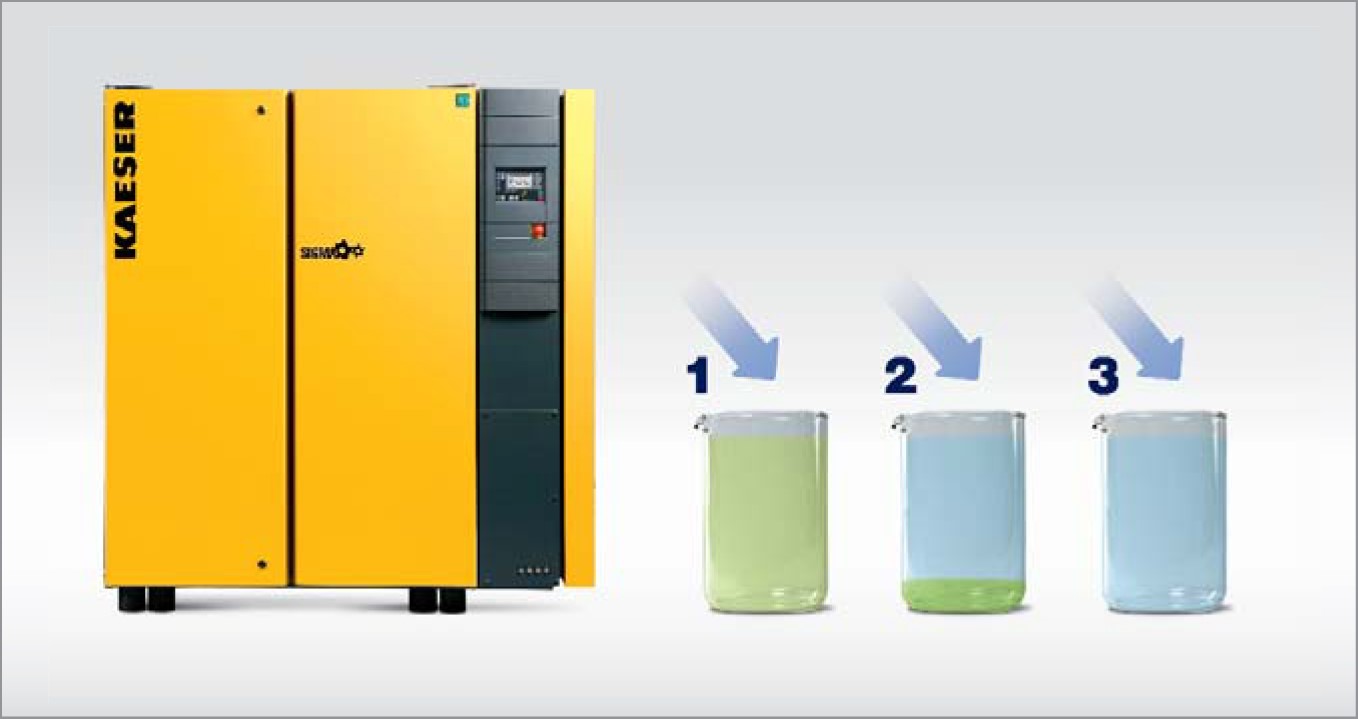
a) Dispersion
The composition of condensate can vary widely. Generally, dispersion occurs in fluid-cooled rotary screw compressors using synthetic coolants, such as Kaeser’s “Sigma fluid S460” for example. This condensate normally has a pH value between 6 and 9 and can be regarded as pH neutral. With this condensate, pollutants drawn in from the atmosphere are captured in a floating layer of oil that is easily separated from the water.
b) Emulsion
A visible sign of emulsion is a milky fluid that does not separate even after several days. This composition often occurs in reciprocating compressors, rotary screw and sliding vane compressors that are used with conventional oils. The pollutants are also captured by the oil.
Because of the thick, stable mixture, oil, water and pollutants such as dust and heavy metals cannot be separated by gravity. If the oils contain ester compounds, the condensate could be aggressive and must be neutralised. Treatment of such condensate is only possible with emulsion splitting units.
3. Specialised condensate removal
Of course, it is possible to collect the condensate and have it disposed of by a specialist company. However these costs are typically between €40 and €150 per m³. In view of the amount of condensate accumulated, treatment would be the more economical approach. This method has the advantage that only approx. 0.25% of the original volume is left over to be disposed of in accordance with environmental regulations.
Acces Kaeser machines for condensate removal.
4. Condensate removal process
a) For dispersions
A triple chamber separator comprising two initial separating chambers and an activated carbon filter chamber is used to treat this kind of condensate (fig. 2). The actual separation process takes place under the force of gravity. The oil layer floating on the surface of the fluid in the separating chamber is skimmed off into a container and disposed of as waste oil.
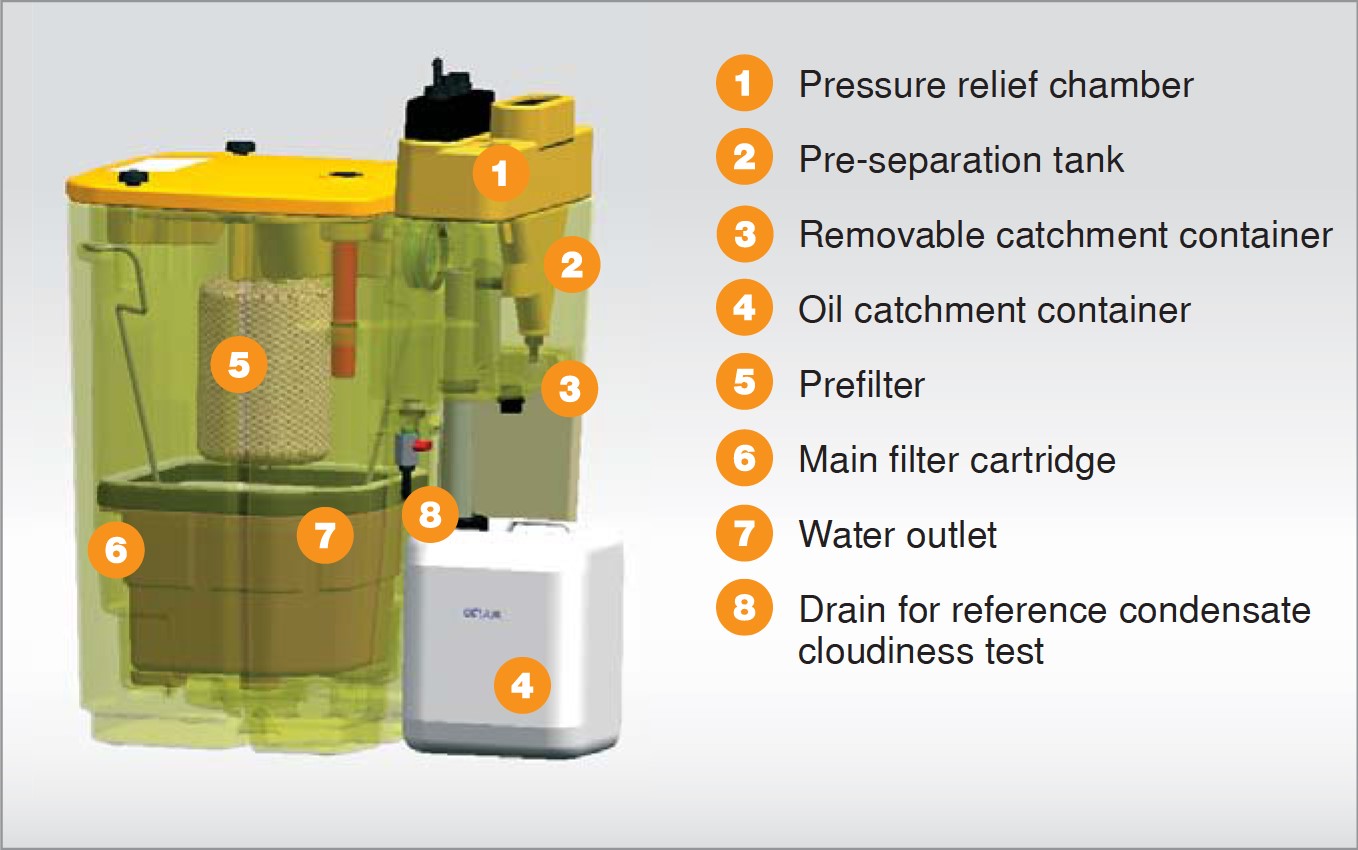
The remaining water is then filtered in two stages and can be disposed of as waste water. This process saves up to 95 % of the costs involved if a specialised company were to dispose of the condensate. These separators can be supplied to handle compressor air deliveries of up to 105 m³/min. If needed, several separators can be connected in parallel.
b) Eliminarea condensului pentru emulsii
In general, two types of separator are used for the treatment of stable emulsions: Membrane separating systems work on the principle of ultra-filtration using the so-called cross-flow process. During this process, pre-filtered condensate flows across the membrane. A portion of the condensate permeates the membrane and leaves the separator as clean water that can be disposed of as waste water.
The second type uses a powdered splitting agent. This encapsulates oil particles, forming easily filtered macro-flocs. filters of a defined pore size reliably retain these flocs. The drained water can be disposed of as waste water.