Compressed air systems typically comprise multiple compressors of similar or various sizes.
As effective control is essential to ensure efficient system operation, a master controller is needed to coordinate the operation of individual machines: Compressed air production is precisely matched to suit actual compressed air demand and maximum efficiency is ensured at all times.
Within the scope of regulation and control technology, the systems generally referred to as compressor controllers should be considered as regulating systems. These are chiefly divided into four groups:
1. Cascade control
The classic method of controlling a group of compressors is cascade control. Each individual compressor is assigned lower and upper pressure set points that either add or subtract compressor capacity to meet system demand.
If several compressors are to be coordinated, this strategy results in a cascaded, or stepped control system.
Când cererea de aer comprimat este scăzută, funcționează un singur compresor iar presiunea crește și fluctuează în intervalul superior între presiunea minimă (pmin) și presiunea maximă (pmax) a acestui compresor.
Când cererea de aer comprimat crește, presiunea scade și sunt pornite alte compresoare pentru a o satisface (fig. 1).
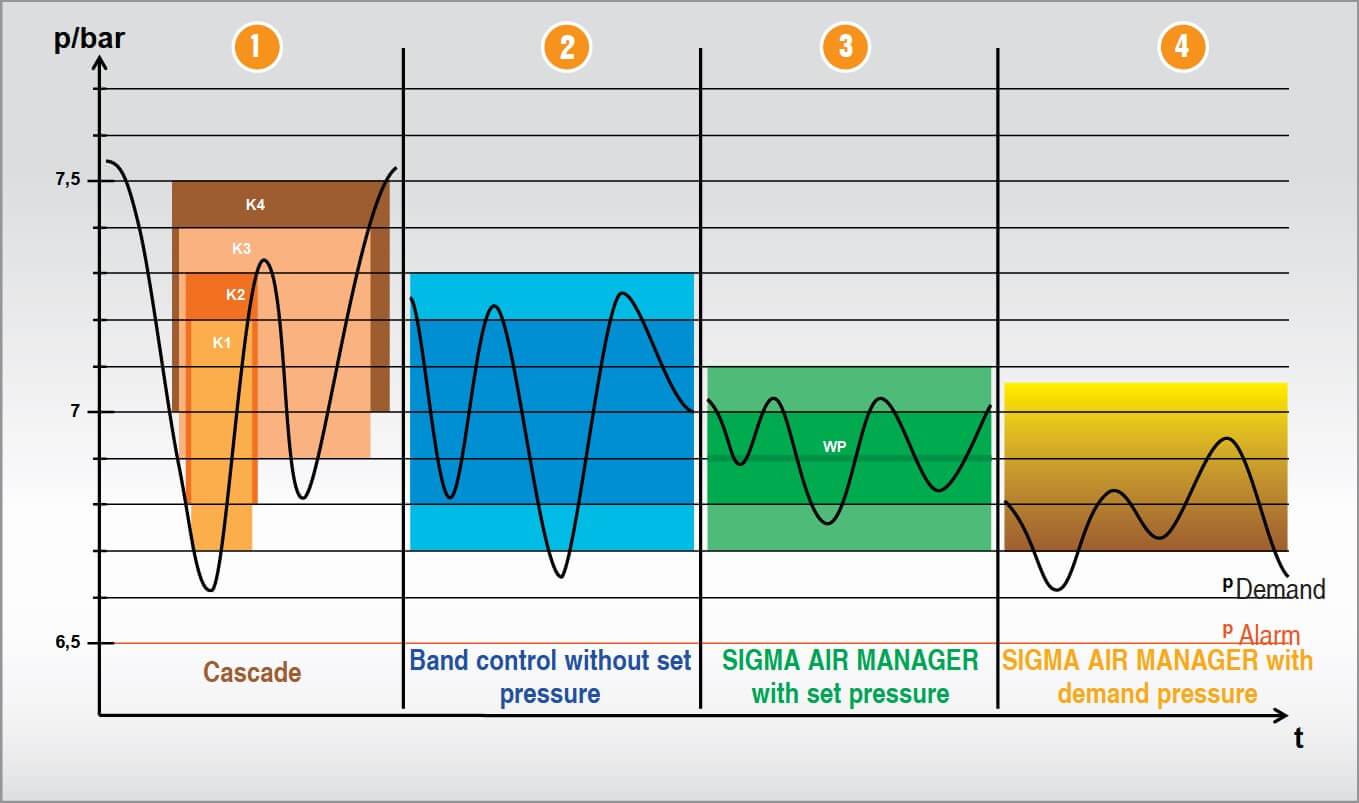
Aceasta are ca rezultat o variație totală de presiune relativ mare cu valori maxime cu mult peste presiunea nominală de lucru, mărind importanța pierderilor de aer prin neetanșeități și a pierderilor de energie aferente; pe de altă parte, în cazul în care consumul este mare, presiunea scade mult sub valoarea presiunii nominale de lucru și rezerva de presiune din sistem este redusă.
Depending on whether conventional membrane pressure switches, contact pressure gauges or electronic pressure sensors are used as measurement sensors, the control system pressure spread will be very large due to the individual allocation of the compressors to a certain pressure range.
The more compressors that are in use, the larger the pressure ranges overall. This leads to ineffective regulation with the already mentioned higher pressures, leakages and energy losses.
Cascade regulating systems should therefore be replaced by other regulation methods when used in combination with more than two compressors.
2. Pressure band control
In contrast to cascade regulating systems, pressure band control (fig. 1 Column 2) enables co-ordination of multiple compressors within a single defined pressure range.
This allows the pressure range within which the compressed air station is regulated to be kept relatively narrow.
a) Simple pressure band control
Simple versions of pressure band control are, however, not able to co-ordinate operation of compressors of different sizes; they therefore do not meet the requirements to cover peak load demand in compressed air networks that have to accommodate continuously fluctuating demand conditions.
This method was therefore replaced by a system that, based on periods of pressure fall and rise, aims to control the appropriate compressors and to therefore cover the compressed air peak load demand. This regulation approach does however have a relatively large pressure band spread (fig. 2).
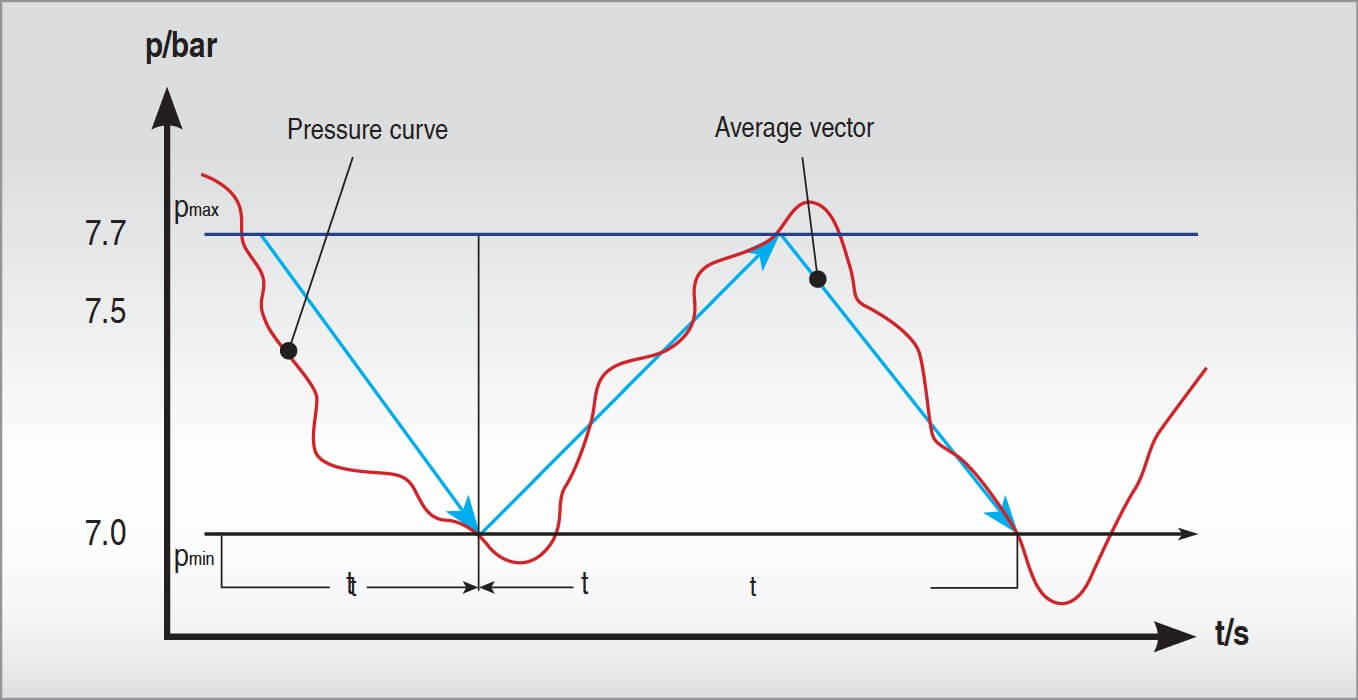
Moreover, similar to cascade control, the reactions of the compressors and the compressed air network are not taken into consideration, which results in a shortfall of the minimum possible pressure dew point. It is therefore necessary to maintain a safety distance between the minimum required pressure and the lowest switching pressure of the regulation system.
b) Set pressure oriented pressure band control
Set pressure oriented pressure band control introduced a signifi cant key improvement (fig. 1, Column 3).
This method strives to maintain a certain set pressure and, according to compressed air demand, can control compressors of different sizes.
The key advantage of this regulation variant is that it allows the average operating pressure of the compressed air system to be significantly reduced and therefore helps to achieve considerable energy and cost savings.
3. Demand pressure control
Demand pressure control (fig. 1, Column 4) is currently the most favourable regulation method. With this variant, no minimum and maximum pressure is specified, just the lowest possible working pressure at which the pressure sensor measurement point is not undershot (fig. 3).
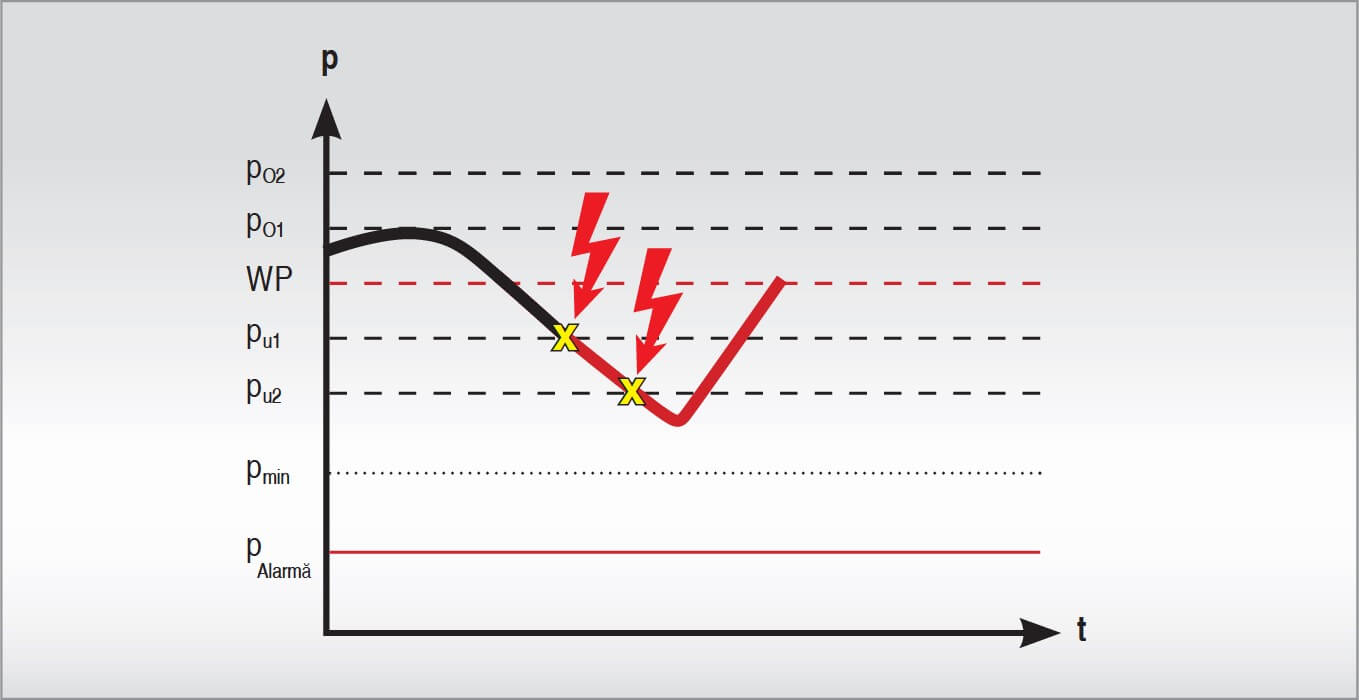
Taking into consideration all possible losses caused by pressure increase, start-up time, reaction and idling periods, as well as speed control of individual units, this regulation method determines optimum performance with regards to switching and compressor selection.
Thanks to recognition of individual reaction times, the system is able to ensure that the minimum allowable demand pressure is not undershot (fig. 4).
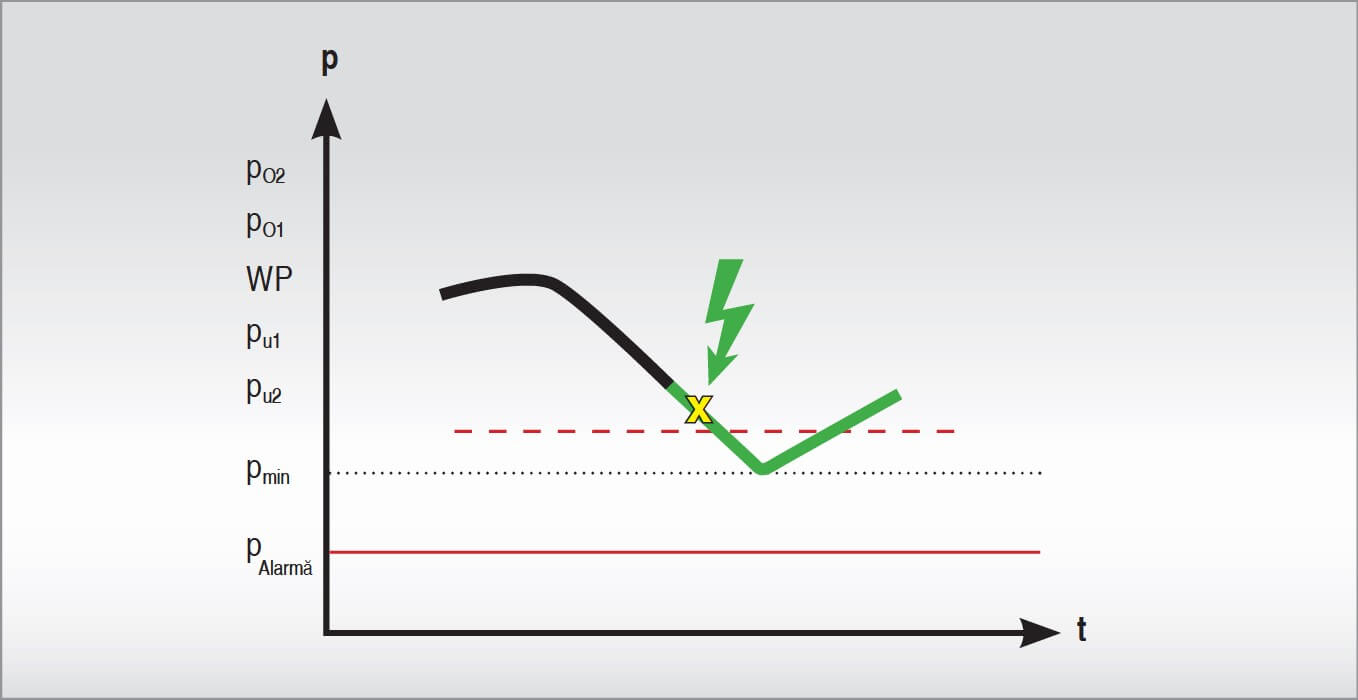
With this new variant of adaptive 3Dadvance Control, which is included in the SIGMA AIR MANAGER 2 master controller, it is possible to reduce energy consumption even further than with set pressure oriented pressure band control.
Moreover, the potential for undershooting of the preset pressure level is eliminated and it is surprisingly simple for the operator to adjust the demand pressure control him-/herself.