With meticulous compressed air system optimisation, it is possible to save more than 30% of average European compressed air costs for industrial businesses. Approximately 70 to 90 % of these costs are accounted for by energy demand.
In view of ever-increasing energy prices, it is therefore more important than ever for users to determine and implement the most efficient compressed concept for their business. Using the optimisation calculation from the KAESER Energy Saving System (KESS), it is possible to compare various system solutions for the specific-application in question and identify the most efficient solution.
For new systems, the completed design questionnaire provides the basis for this calculation. For existing air systems the calculation is based on the characteristic daily profile determined by an compressed air demand analysis (ADA).
1. Computer-aided analysis
Before an existing air supply system can be optimised, all the technical data relating to it and any possible new alternatives are entered into the KESS software. KESS then identifies the optimum system design and calculates the potential cost savings.
Moreover, the momentary power consumption at a defined air demand, including all losses, is also calculated. It is also possible to establish a precise picture of the specific power profile of the air system throughout the entire running period (fig. 1).
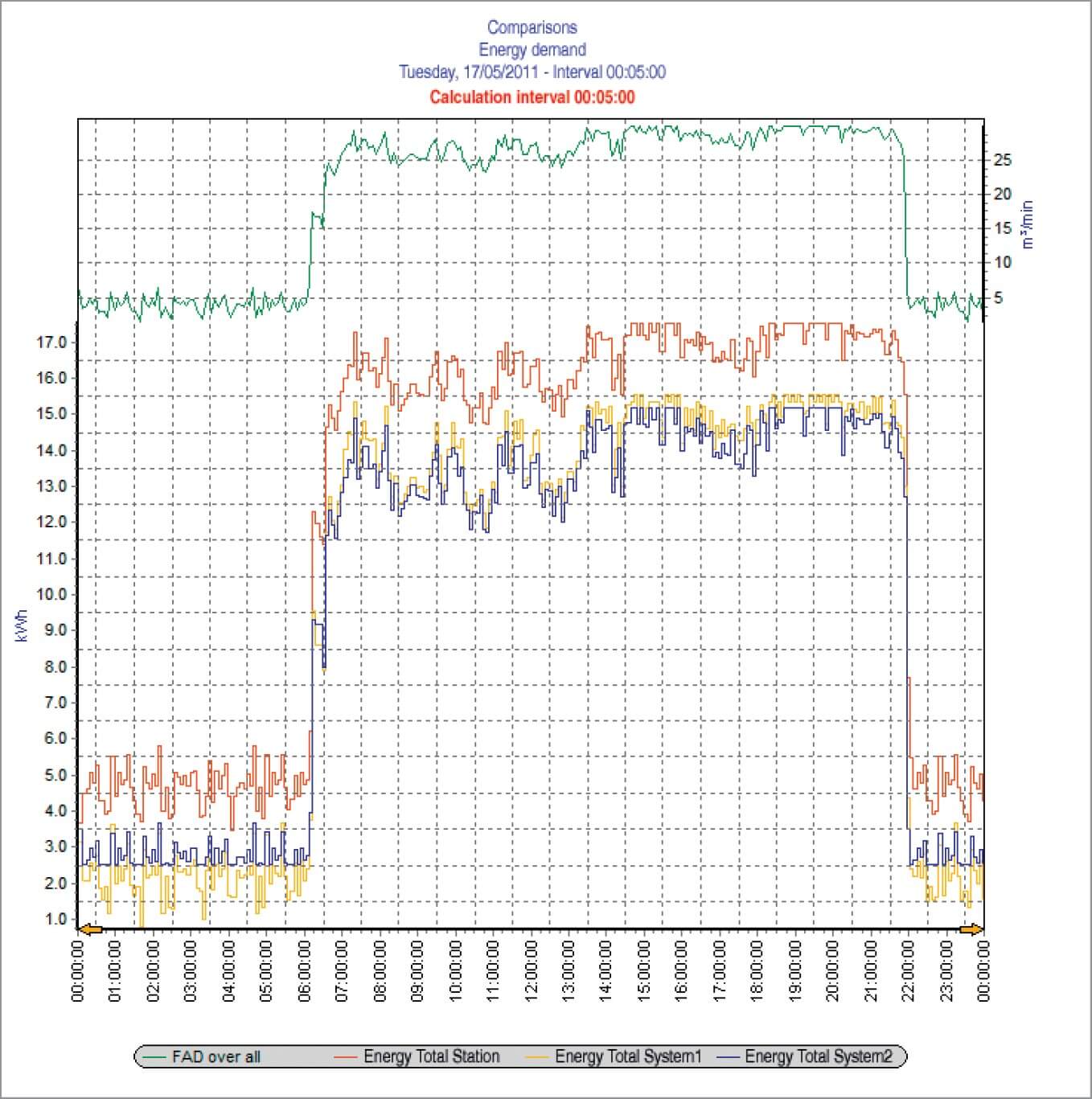
This means that any weak points in partial load operation can be detected in advance and remedied. The overall result is a clear statement of the potential cost savings and amortisation period.
2. The combination of compressors is what matters
In most cases a precisely coordinated configuration of compressors of different capacities has proven to be the best solution. The mix generally consists of large capacity base load and standby compressors combined with smaller peak load machines.
The purpose of the central compressor controller is to ensure the lowest specific power consumption. To do this, the controller must be able to automatically select the most suitable combination of base and top compressors; a maximum of 16 compressors working in a pressure band of only 0.2 bar.
Intelligent master control systems such as KAESER’s SIGMA AIR MANAGER meet these needs and enable highly sophisticated system control. In addition, they can be connected to centralised control systems, as well as other compressors and additional components such as condensate drains, dryers, etc. and allow data exchange via a powerful bus system.
3. Structural optimization of compressors
A newly designed or modernised air supply system should make optimum use of the space in which it is to be installed. Modern design systems such as those used by KAESER provide worthwhile support in this regard. During the design process they not only make use of floor plans and P & I diagrams, but also use advanced 3-D computer-generated plans and animations.
This means that it is often possible to take advantage of efficient compressor air-cooling despite cramped conditions in the compressor room. Air-cooling saves between 30 and 40% of the costs normally associated with watercooled systems (figs. 2a to c).
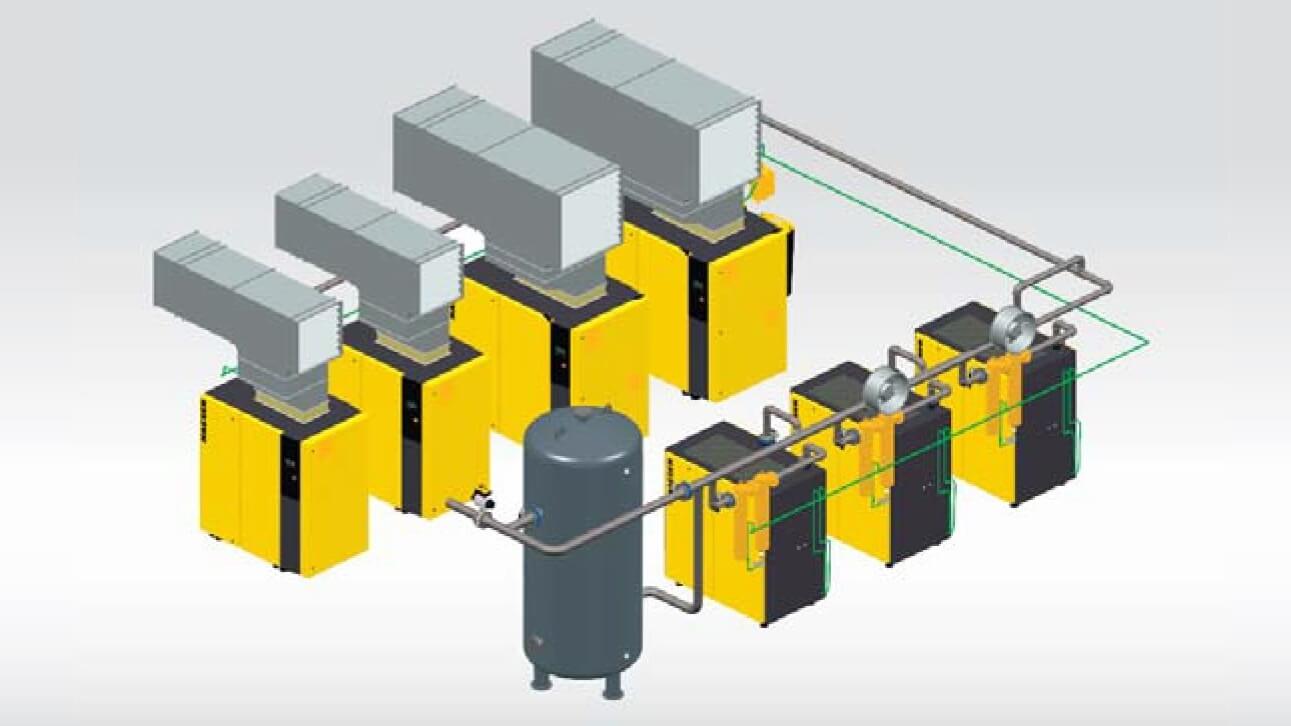
4. Operational optimisation and controlling
In order to ensure compressed air system efficiency over the long-term, it is essential to have an optimised cost/ use ratio and complete transparency via an effective control system. This is where KAESER’s integrated PC-based SIGMA CONTROL comes into to its own, as it features five pre-programmed control modes and is able to gather data and transfer it back to a data network.
At the master control level a further industrial computer is used: the SIGMA AIR MANAGER. Its task, as well as appropriate control and monitoring of the air supply system, is to collect all relevant data and pass it on to a computer network (Ethernet).
This can take place via Internet or via the SIGMA CONTROL CENTRE centralised control software. Together with the SIGMA AIR CONTROL visualisation system, this PC-installed software can display a list of all the air compressors and their key operational data. This shows at a glance whether the system is functioning correctly, whether maintenance or alarm messages are activated and how high system pressure is.
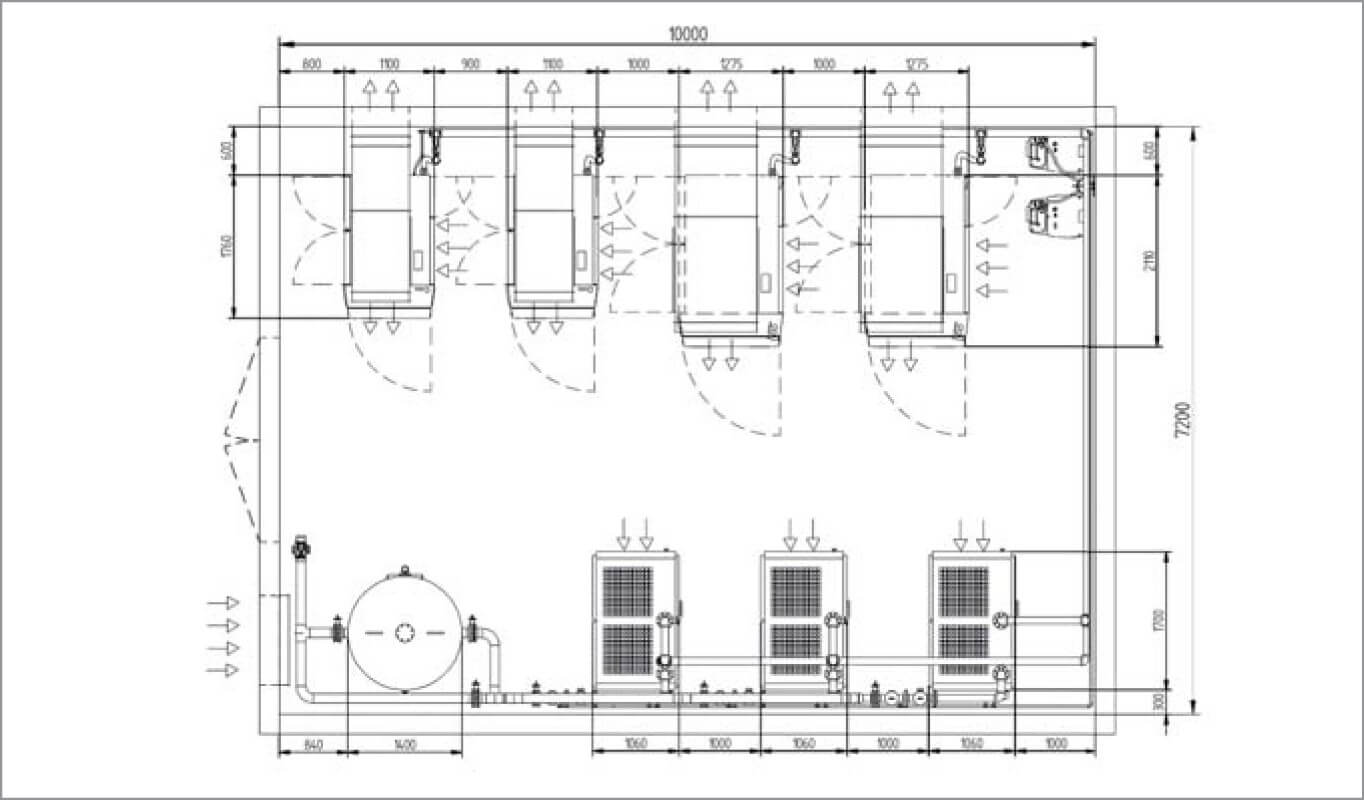
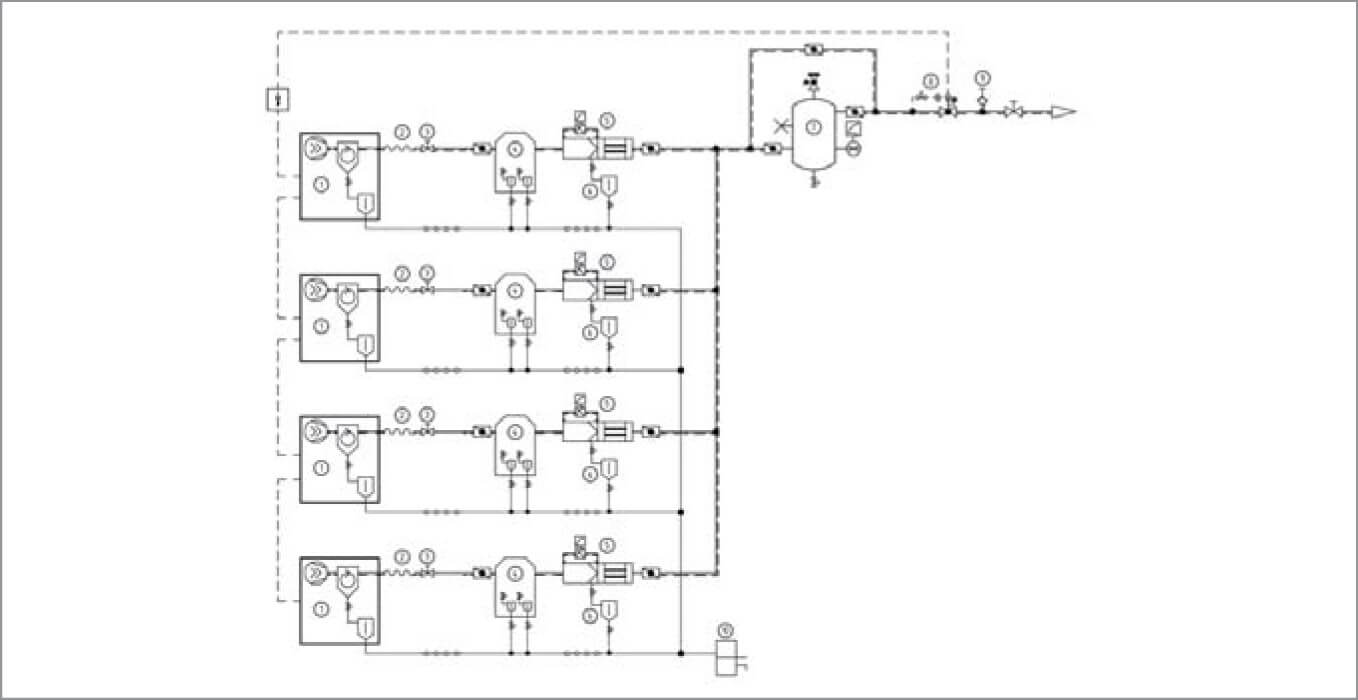